Automated Guided Vehicles Do the Heavy Lifting
Automated Guided Vehicles Do the Heavy Lifting
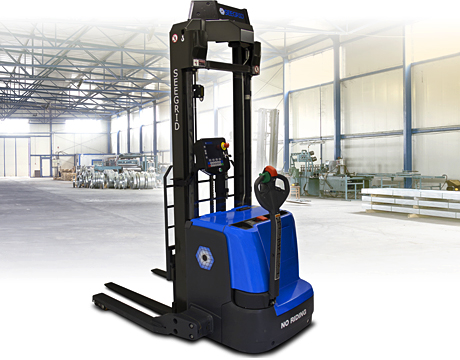
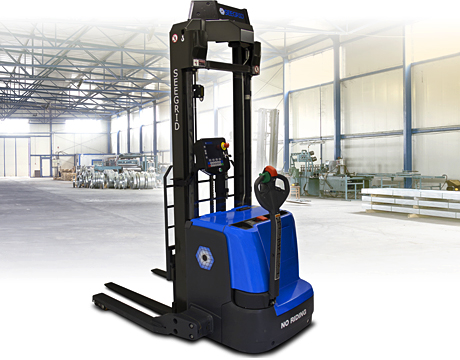
Automated guided vehicles serve as unmanned pallet trucks that operate with much higher precision than human operators. Image: Seegrid.com
Human beings aren’t perfect, which is why we make mistakes, hurting ourselves on the job, or mishandling equipment that damages products and the bottom line.
Take, for example, palletized goods, which are hustled through manufacturing plants and distribution facilities 24/7. Pallets are often dropped, lifted, and pushed across hard floors. Pallet damage often results in damaged products and “unsaleable” merchandise that averages about 1% of gross sales for retailers and distributors.
An innovative solution to this problem is automated guided vehicles (AGV) that serve as unmanned pallet trucks and tow tractors that operate with much higher precision than human operators.
Vision-Guided Navigation
What makes AGVs so special? Sophisticated, vision-guided technology.
Seegrid Corporation, Pittsburgh, PA, is a manufacturer of AGVs for the material-handling industry, including robotic pallet trucks, tow tractor, and walkie stackers. These vehicles are equipped with range-finding stereo cameras that record and store thousands of features along the route, allowing the AGV to “remember” the route by replaying the recorded features.
This type of vision-based evidence-grid technology, an application of probabilistic volumetric sensing, was invented and initially developed by Dr. Hans Moravec at Carnegie Mellon University.
Seegrid has built upon this technology with its AGVs, using stereo cameras to construct 360-degree maps of the environment. The images are analyzed in real time to identify features, and their locations, in three-dimensional space. Five pairs of stereo cameras operate concurrently to analyze thousands of interest points per second, with a margin of error of only one to two inches.
“This allows the vehicles to be deployed easily,” says Mitchell Weiss, chief operating officer for Seegrid. “They are walked through the path once to build the map, and then they repeat the route. Because of the high density of map data, they can maintain precise navigation even in changing environments.”
Highly Integrated Systems
From an engineering perspective, AGVs are highly integrated systems. They start out as a basic chassis. Because the optical equipment is so sensitive, Seegrid engineers must devise methods that allow these high-precision components to be integrated with the chassis, and also withstand harsh shock and vibration conditions.
“To accomplish this we have designed rugged mechanical components, which can be adjusted or adapted to the truck chassis at time of manufacture,” says Weiss. “Camera-to-camera and camera-to-vehicle fine-tuning is accomplished with software.”
The size of components is very diverse, ranging from customized miniature cameras to one-half-inch-thick steel plate to batteries that weigh 1,000 pounds. This requires a variety of manufacturing environments, including near-clean rooms with special calibration tools for the cameras, ESD-controlled environments for electronics assembly, overhead cranes and lifts for the trucks, and simulated warehouse environments (cold, dim) for testing.
“We have also added more time for AGV burn-in than is normal for the industry, to detect infant mortality in hydraulic system seals, bearing contamination, and other infant issues,” adds Weiss. “We have also improved battery monitoring to compensate for the lack of a driver, who can notice changes in vehicle performance duringa shift.”
Future Plans
The most expensive part of operating a truck is the cost of the driver. This cost includes wages and benefits, accidents, injury, lost time, and errors. Also, human drivers cannot operate without breaks for instruction, food, stretching, etc. In comparison, robotic pallet trucks, priced at $85,000, operate at significantly higher duty cycles, improving capital performance.
“AGVs are the ultimate electric vehicle,” says Weiss. “Unlike the cars we drive, they really can run 24/7, do it for up to 10 years, emit zero emissions, and tow up to 10,000 pounds. All of this comes in a package size that fits in the bed of a pickup truck.”
Seegrid’s vision-guided AGVs currently operate from point to point along planned routes. “Company engineers are continually developing new methods for improving camera performance, using field data collected from hundreds of deployed systems,” says Weiss.
For example, the company has just developed a new walkie stacker that automatically picks, drops, stacks, and puts away loads up to 72 inches, at a maximum load capacity of 3,500 pounds—ideal for automatic lane building or deep lane storage at dock and staging locations.
Mark Crawford is an independent writer.
AGVs are the ultimate electric vehicle.Mitchell Weiss, COO, Seegrid