Wearable Patch Offers Voice to the Voiceless
Wearable Patch Offers Voice to the Voiceless
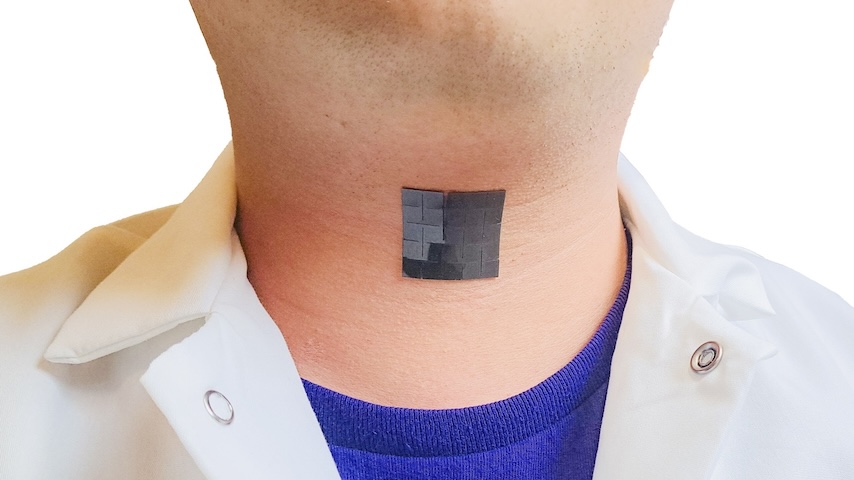
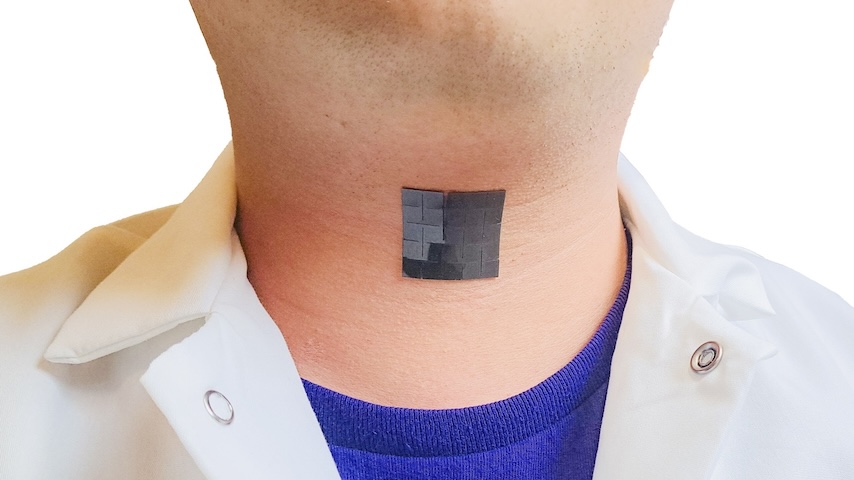
A thin self-powered patch can sense the movement of laryngeal muscles and translate those movements into audible speech.
Giving two-hour-long lectures twice a week can really wear on your voice—something that Jun Chen, an assistant professor of bioengineering at the UCLA Samueli School of Engineering and Wearable Bioelectronics Research Group lead, realized as his lecture schedule grew after coming to UCLA in 2019.
After Chen’s team developed a glove fitted with sensors that allowed for real-time translation of American Sign Language into speech through a smartphone app in 2020, he realized that they could use some of the same concepts they had already developed to create a device that could help people with voice disorders.
The result is a 1.2-square-inch flexible patch that is just 0.06 inches thick and weighs 7 grams. An adhesive on one side of the patch allows it to stick right on an individual’s skin, right over the larynx.
Once attached, this bioelectric system can detect laryngeal muscle movement and translate those signals into audible speech.
A team of six students has been working on this project with Chen for the last year and a half. “Speaking without vocal folds using a machine-learning-assisted wearable sensing-actuation system,” was published in Nature Communications in March.
Underlying tech
What makes this patch possible is a fundamental new working principle that Chen’s team developed in 2021 called magnetoelasticity in a soft matter system. Simply put, it converts motion into electric signals that can power or send signals to sensors.
Their initial goal was to develop a waterproof bioelectronic device that wouldn’t need an encapsulation layer, which could degrade a device’s performance or sensitivity, Chen explained.
Although magnetoelasticity is typically observed in rigid metals or metal alloys, Chen’s team realized that if they mixed some magnetic nanoparticles with a polymer matrix, the resulting soft composite would still show a decrease in its magnetic flux density (measure of force)—but the required mechanical pressure would be greatly reduced from the 20 megapascals needed for metals to just 100 kilopascals.
“That pressure could be derived from finger bending, respiration, or other biomechanical pressures,” Chen explained. “So, we took this a further step to put this soft composite on a magnetomechanical coupling layer, or MC layer for short, so that means we can apply mechanical pressure or induce magnetic field variations to realize a mechanical to magnetic conversion.”
On top of that soft composite goes a magnetic induction layer, or MI layer, so that when pressure is applied to the MC layer, the MI layer picks up the magnetic field variation and generates a current in the internal circuitry, Chen said. “We call this a magnetoelastic generator, or MEG for short. So, this is a fundamentally new platform technology that we developed in our lab, which is able to realize biomechanical pressure to electric conversion,” he continued, noting that a device using these components is also intrinsically waterproof.
Translating signals
The device's two main components are for sensing and actuation. “For the sensing component, we used the MI layer and MC layer to convert those muscle vibrations into electricity,” Chen explained.
Those electrical signals are then translated into speech signals with the help of a machine-learning algorithm. The next part of the device is an actuation component, which translates those speech signals into an audible voice.
Become a Member: How to Join ASME
Both components are made of a layer of biocompatible silicone compound polydimethylsiloxane (PDMS) and a magnetic induction layer of copper induction coils, with the induction layers facing inward. In between the two components is an MC layer mixed with micromagnets to create a magnetic field.
During tests on eight adult volunteers, the researchers compiled data on laryngeal muscle movement when speaking both aloud and voicelessly, to ensure that the signals would match regardless of the user’s ability to speak. That information helped them create the machine-learning algorithm to translate those motions into words and thus far, the system’s prediction accuracy is around 94.68 percent.
Work ahead
Now that the team has a working prototype, next steps will involve increasing the device’s sensitivity, accuracy, and vocabulary, and improving both user comfort and the patch’s adhesion ability.
“Typically, the human voice has a frequency range from 20 hertz to 2,000 hertz, so we need to make sure the device has a wider range response to the frequency vibration,” Chen added.
The technology behind this device could be used for other applications, such as monitoring devices to track anything from heart rate to muscle velocity, blood pressure, or respiration, he explained. It could even be used as a wireless interface that humans could use to operate machines or electronics. The researchers are exploring a range of these possibilities as well.
Thankfully, cost won’t be quite as much of a barrier for the voice patch as many other biomedical devices often face, as the materials used to make the patch are relatively cheap.
“This is still lab scale research, but we are trying to scale up and optimize the translation accuracy,” Chen said. “We hope in the following three to five years that we can make this commercially available.”
Louise Poirier is senior editor.