Laser Welding Could Improve Solar Module Recyclability
Laser Welding Could Improve Solar Module Recyclability
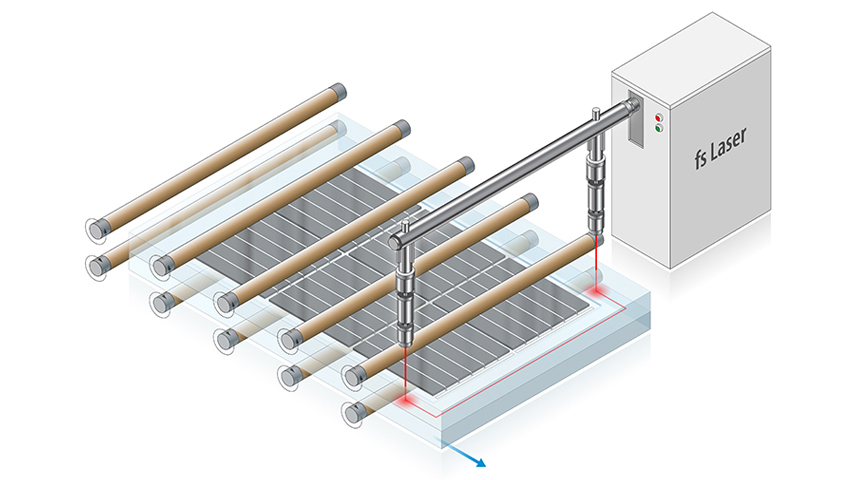
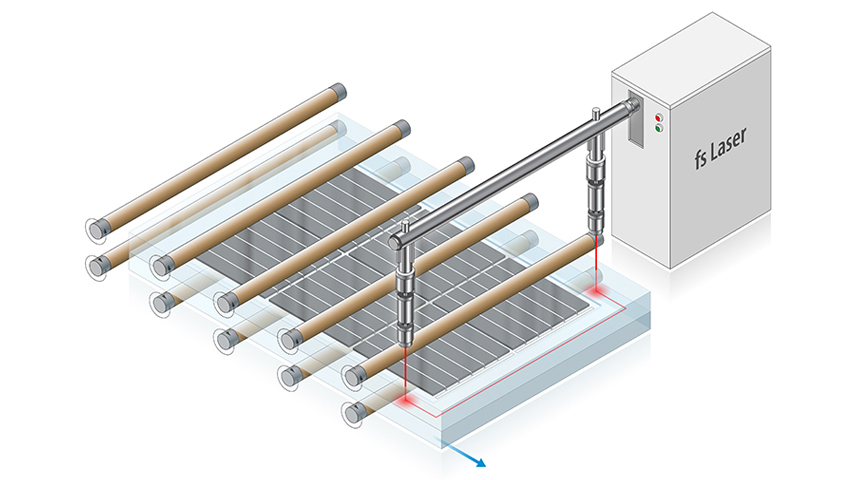
Solar panels are laminated using plastic sheets, which are tough to recycle. A new method eliminates the plastic.
Solar power is booming, and new solar farms are springing up in many places. But engineers are already thinking about the end of life for these photovoltaic panels. One material that is giving them headaches: plastic.
“Most recyclers will confirm that the polymers are the main issue in terms of inhibiting the process of recycling,” said David Young, senior scientist and group manager for the High-Efficiency Crystalline Photovoltaics group in the Chemistry and Nanoscience department at National Renewable Energy Laboratory (NREL) in Boulder, Colo.
Manufacturers protect the photovoltaic material from the elements by laminating polymer sheets on the semiconductor material that produces electricity, and all that is sandwiched between glass panes. When it’s time to recycle the panels, removing the plastic requires several steps which slow down the efficiency of the recycling process.
“Polymers also tend to degrade in the field, which makes panel recycling more difficult because these layers are hard to remove,” he said.
Editor's Choice: Green Power Employment Outlook
Young was intent on creating a better way to recycle solar modules by redesigning their structure to completely remove polymers.
His “aha!” moment came when he realized that instead of plastic sheets, the solar panels could be sealed off by welding the glass panes to each other using a femtosecond laser. The welded glass would be strong enough to survive harsh field conditions. At the end of their lifespans, laser-welded modules can simply be shattered—the glass and metal wires running through the solar cells can be easily recycled and the photovoltaic silicon reused.
Femtosecond lasers are the fastest, highest-precision lasers used in manufacturing today. Because the laser pulses are so short (there are 1 million billion femtoseconds in a full second), they can cut complex shapes or weld without the heat moving beyond the point of contact with the laser, eliminating any heat-affected zones in the surrounding material.
More About Solar Power: New Method Prints Perovskite Solar Cells at Scale
The first question to be answered, noted Young, was would the glass/glass weld be strong enough to survive outdoor conditions? The team partnered with Trumpf, a laser manufacturer based in Ditzingen, Germany, to leverage their welding expertise in testing this idea. They used a COMSOL finite element model of a module under a static load of 5,400 Pa to show that the measured critical stress intensity factor of the welds is strong enough to not crack under normal operating conditions.
“Femtosecond laser glass/glass welding has an interesting feature that makes the welds very strong,” Young said. “The very short pulse duration of the femtosecond laser pumps so many photons into the area of focus that the optical absorption properties of the glass change, such that most of the photons are absorbed.”
Because the focus is at an interface between two sheets of glass, the absorbed photons melt the glass, but no molten glass is evaporated to the surrounding area—it is contained between the glass sheets. “This lack of evaporation of the molten pool allows the glass to cool with no internal stress, making the stress-free weld almost as strong as the surrounding glass,” Young said.
This type of glass weld can be used on any type of solar materials—silicon, perovskites, or cadmium telluride—because the heat of the weld is confined to the point of welding and does not alter the surrounding material.
Green Workforce: The Fight to Decarbonize Needs Solar Workers
“However,” Young said, “not having the polymers between the sheets of glass requires welded modules to be much stiffer. With proper mounting and a modification to the embossed features of the rolled glass, a welded module can be made stiff enough to pass static load testing.”
Femtosecond laser glass/glass welding is already used in fields such as laser head production and medical devices. NREL believes this research is the first to use a femtosecond laser to form glass/glass welds in a solar module.
“If our process can work on large area solar modules, vacuum insulated glass units might also benefit,” Young said.
Young is currently writing proposals to extend their work to larger samples and to perform dynamic load testing on the welds.
“Our goal is to take this technology to market and to inspire new designs for solar modules that will make them more durable, less expensive, and easier to recycle,” he said.
Mark Crawford is a technology writer in Corrales, N.M.
“Most recyclers will confirm that the polymers are the main issue in terms of inhibiting the process of recycling,” said David Young, senior scientist and group manager for the High-Efficiency Crystalline Photovoltaics group in the Chemistry and Nanoscience department at National Renewable Energy Laboratory (NREL) in Boulder, Colo.
Manufacturers protect the photovoltaic material from the elements by laminating polymer sheets on the semiconductor material that produces electricity, and all that is sandwiched between glass panes. When it’s time to recycle the panels, removing the plastic requires several steps which slow down the efficiency of the recycling process.
“Polymers also tend to degrade in the field, which makes panel recycling more difficult because these layers are hard to remove,” he said.
Editor's Choice: Green Power Employment Outlook
Young was intent on creating a better way to recycle solar modules by redesigning their structure to completely remove polymers.
His “aha!” moment came when he realized that instead of plastic sheets, the solar panels could be sealed off by welding the glass panes to each other using a femtosecond laser. The welded glass would be strong enough to survive harsh field conditions. At the end of their lifespans, laser-welded modules can simply be shattered—the glass and metal wires running through the solar cells can be easily recycled and the photovoltaic silicon reused.
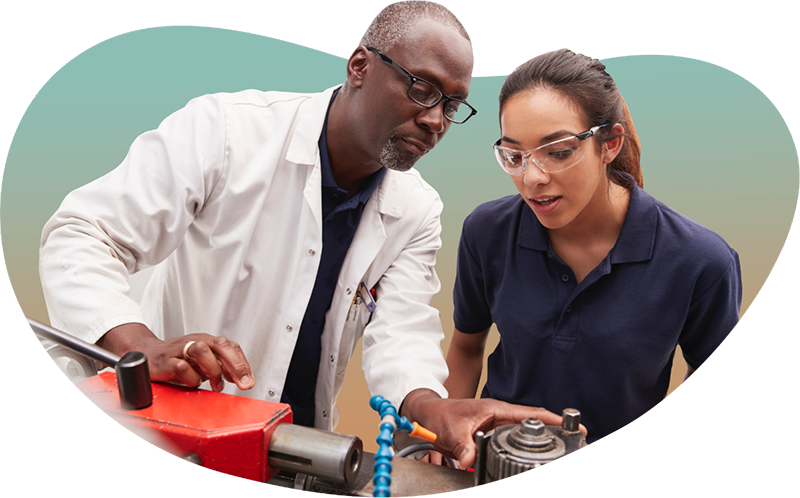
Boost Your Career With ASME
Whether you’re an experienced professional or just starting your career, ASME’s membership community, resources and tools can help you with your lifelong journey.
Femtosecond lasers are the fastest, highest-precision lasers used in manufacturing today. Because the laser pulses are so short (there are 1 million billion femtoseconds in a full second), they can cut complex shapes or weld without the heat moving beyond the point of contact with the laser, eliminating any heat-affected zones in the surrounding material.
More About Solar Power: New Method Prints Perovskite Solar Cells at Scale
The first question to be answered, noted Young, was would the glass/glass weld be strong enough to survive outdoor conditions? The team partnered with Trumpf, a laser manufacturer based in Ditzingen, Germany, to leverage their welding expertise in testing this idea. They used a COMSOL finite element model of a module under a static load of 5,400 Pa to show that the measured critical stress intensity factor of the welds is strong enough to not crack under normal operating conditions.
“Femtosecond laser glass/glass welding has an interesting feature that makes the welds very strong,” Young said. “The very short pulse duration of the femtosecond laser pumps so many photons into the area of focus that the optical absorption properties of the glass change, such that most of the photons are absorbed.”
Because the focus is at an interface between two sheets of glass, the absorbed photons melt the glass, but no molten glass is evaporated to the surrounding area—it is contained between the glass sheets. “This lack of evaporation of the molten pool allows the glass to cool with no internal stress, making the stress-free weld almost as strong as the surrounding glass,” Young said.
This type of glass weld can be used on any type of solar materials—silicon, perovskites, or cadmium telluride—because the heat of the weld is confined to the point of welding and does not alter the surrounding material.
Green Workforce: The Fight to Decarbonize Needs Solar Workers
“However,” Young said, “not having the polymers between the sheets of glass requires welded modules to be much stiffer. With proper mounting and a modification to the embossed features of the rolled glass, a welded module can be made stiff enough to pass static load testing.”
Femtosecond laser glass/glass welding is already used in fields such as laser head production and medical devices. NREL believes this research is the first to use a femtosecond laser to form glass/glass welds in a solar module.
“If our process can work on large area solar modules, vacuum insulated glass units might also benefit,” Young said.
Young is currently writing proposals to extend their work to larger samples and to perform dynamic load testing on the welds.
“Our goal is to take this technology to market and to inspire new designs for solar modules that will make them more durable, less expensive, and easier to recycle,” he said.
Mark Crawford is a technology writer in Corrales, N.M.
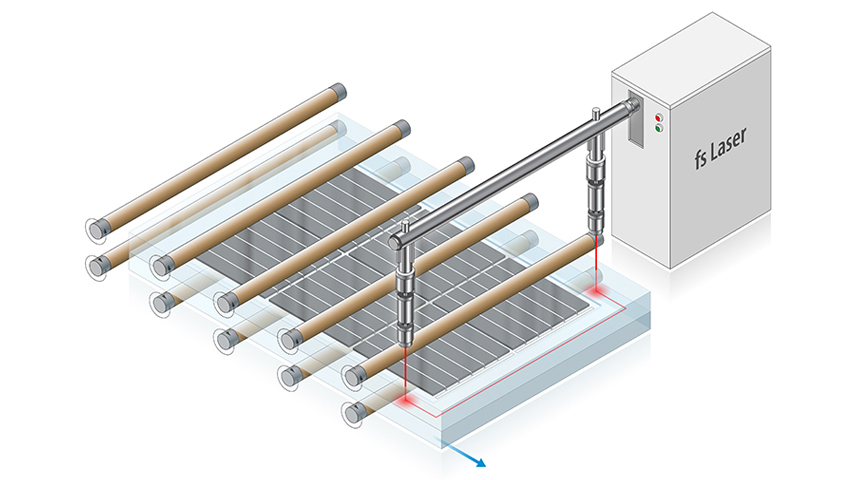
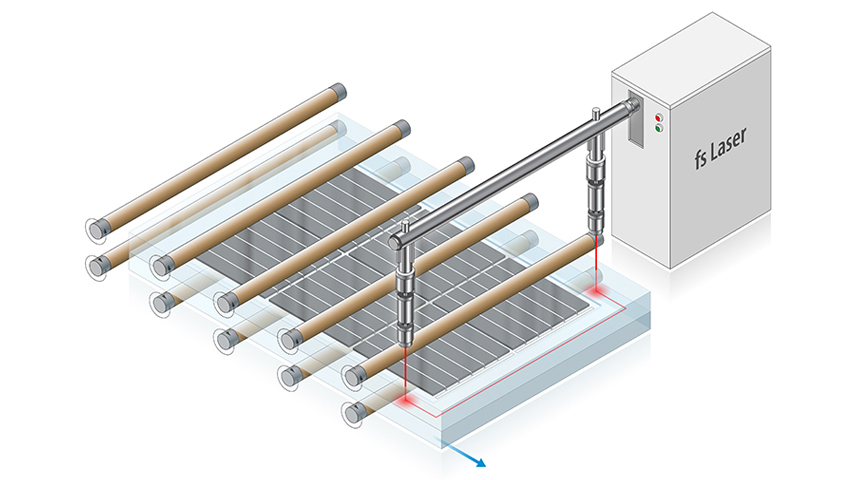