New Method Prints Perovskite Solar Cells at Scale
New Method Prints Perovskite Solar Cells at Scale
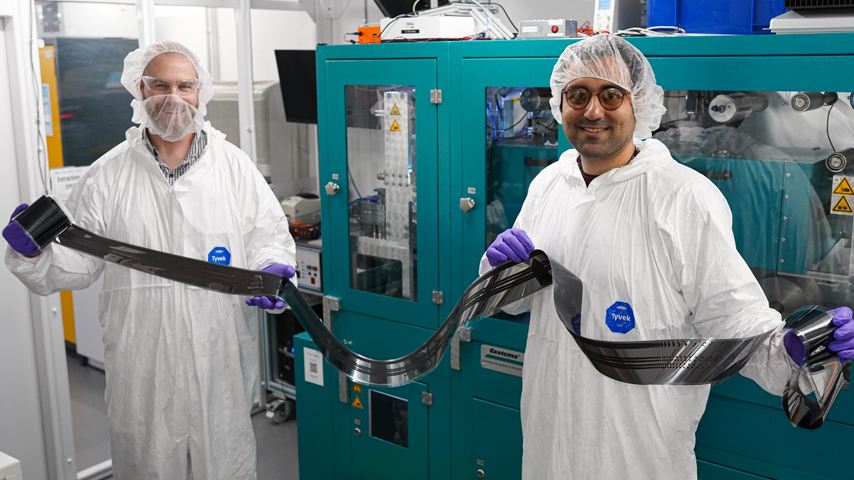
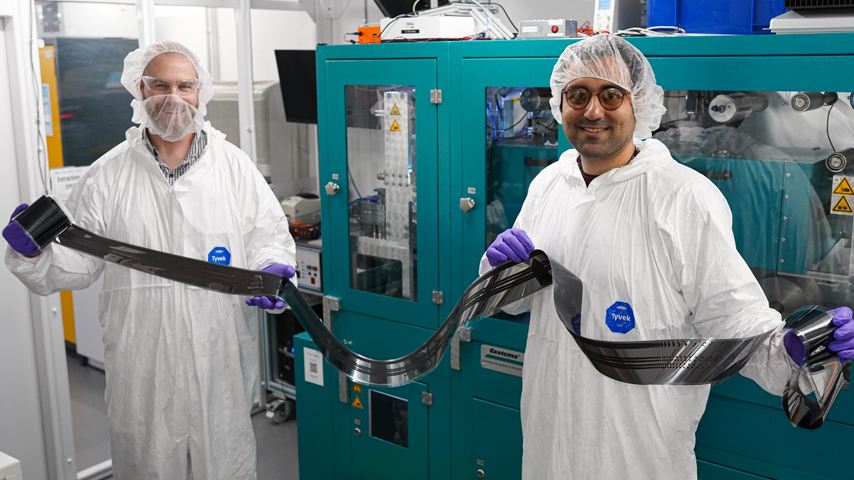
Engineers at Swansea University in Wales have developed a method to fully print complete perovskite solar cells—a process that is over 100 times faster than conventional cell production.
For solar power generation, silicon photovoltaics is a well-established technology that is on a rapid growth track. However, these solar-panel systems are energy-intensive to manufacture, rigid and heavy, time-intensive to install, and susceptible to damage, especially during transport.
As a viable alternative to standard solar cells, perovskite photovoltaics have developed rapidly in research labs with the promise of easy manufacture and high performance. Though promising, the ability to manufacture perovskite photovoltaics through large-scale printing and coating processes is still problematic and time- and cost-intensive. For example, constructing a perovskite device today requires the application of a precious metal electrode (typically gold) using an expensive and slow evaporation process after the device has been printed, a process that is virtually impossible to scale up at reasonable speed and cost.
Now a team of researchers from the SPECIFIC Innovation and Knowledge Center at Swansea University in Wales has perhaps solved this manufacturing challenge by developing a slot die coating process that builds all the active layers in a perovskite photovoltaic device, thus fulfilling their goal of feeding plastic film into the printing press at one end and receiving fully working solar cells at the other end.
Combining slot die coating with a roll-to-roll (R2R) process allowed the engineering team to “fully print” perovskite photovoltaics.
The printed perovskite layer generates free electrons from the energy provided by light hitting it. The semiconductor then prevents the perovskite from re-absorbing its electrons, creating the potential for good power conversion efficiency (PCE). However, the researchers still needed to find a way to efficiently extract the electrical charge.
“The key was identifying the right solvent mix, one which dries as a film without dissolving the underlying layer,” said David Beynon, senior research officer at SPECIFIC. “X-ray diffraction analysis showed carbon electrode ink is capable of this when formulated with an orthogonal solvent system. This innovative layer can be applied continuously and compatibly with the underlying layers at a low temperature and high speed.”
The carbon ink was specifically formulated for compatibility with the perovskite material and the slot die coating process by combining conductive carbon particles, polymer binder, and solvent. The combination of polymer and solvent was carefully controlled so that the ink could flow through the coating head to produce continuous electrodes, which are formed when the solvent evaporates leaving the conductive carbon bound together by the polymer binder.
“The biggest challenge was compatibility of materials and compatibility of process,” noted Beynon. “Perovskite is easily degraded by incompatible solvents. Therefore a solvent system for our ink had to be compatible with not only the perovskite active layer but also the sandwiching semiconductors. This solvent and conductive carbon ink system also had to be compatible with the slot die coating system, tailored to have a rheology compatible with narrow channels and process window of slot die coating.”
The final result was an R2R system that printed large volumes of flexible, rollable perovskite solar cells that exited the printing press, ready to generate power. Testing showed these cells produced a stabilized PCE of 10.8 percent (close to the 13 percent to 14 percent PCE range for cells printed using the conventional but more problematic gold electrode method).
Even with a pilot lab-scale printing set-up, the production rate was 115 times higher than that for conventional perovskite solar cells.
What surprised Beynon the most was the stability of the devices. “The lifetime of a perovskite solar cell is a critical concern and was not something we were considering as part of this research,” he explained. “It was a surprise to find that our device structure and printed carbon electrodes improved the stability of the perovskite cells, compared to gold with no encapsulation of the devices.” However, one of the factors driving perovskite degradation is moisture and the carbon electrodes are hydrophobic, effectively providing protection to the active material and thereby increasing the lifetime.
The most exciting aspect of demonstrating entirely roll-to-roll coated perovskite solar cells for the first time is that the success and further improvements to come will be driven by engineering.
“Using large-scale printing equipment is highly dependent upon controlling the process parameters, from the interaction between coating speed and pump flow rate to the use of low flow limit to predict and then control the stable coating window,” he said. “We must continuously print defect-free films as thin as 50 nm—something that is impossible without control and optimization of the substrate handling such as tension control and web guiding of the polyethylene terephthalate (PET) substrate.”
Beynon and his team are working to improve all layers of the device stack, including replacing the perovskite material with the higher-performing multi-cation perovskite materials. This will hopefully lead to higher conversion efficiencies that could approach the typical 17 percent conversion efficiency of domestic solar panels in use today.
The flexibility of these new perovskite solar panels could make them ideal for surfaces that previously could not accept solar cells, such as curved surfaces, roofs, facades, and polytunnels.
“We have achieved printing perovskite solar cells where we feed a plastic substrate into the printing press and take working solar cells out,” said Beynon. “This provides us with a platform that we will use to improve the performance of the cells by changing the device layers, introducing interlayers, and employing higher-performing perovskite chemistry.
“We are also looking forward to producing prototype panels that can be deployed for outdoor testing, demonstrating that these perovskite modules can be used in a real-world environment to generate electricity at low cost.”
Mark Crawford is a technology writer in Corrales, N.M.
As a viable alternative to standard solar cells, perovskite photovoltaics have developed rapidly in research labs with the promise of easy manufacture and high performance. Though promising, the ability to manufacture perovskite photovoltaics through large-scale printing and coating processes is still problematic and time- and cost-intensive. For example, constructing a perovskite device today requires the application of a precious metal electrode (typically gold) using an expensive and slow evaporation process after the device has been printed, a process that is virtually impossible to scale up at reasonable speed and cost.
Now a team of researchers from the SPECIFIC Innovation and Knowledge Center at Swansea University in Wales has perhaps solved this manufacturing challenge by developing a slot die coating process that builds all the active layers in a perovskite photovoltaic device, thus fulfilling their goal of feeding plastic film into the printing press at one end and receiving fully working solar cells at the other end.
Carbon electrode ink
Combining slot die coating with a roll-to-roll (R2R) process allowed the engineering team to “fully print” perovskite photovoltaics.
The printed perovskite layer generates free electrons from the energy provided by light hitting it. The semiconductor then prevents the perovskite from re-absorbing its electrons, creating the potential for good power conversion efficiency (PCE). However, the researchers still needed to find a way to efficiently extract the electrical charge.
“The key was identifying the right solvent mix, one which dries as a film without dissolving the underlying layer,” said David Beynon, senior research officer at SPECIFIC. “X-ray diffraction analysis showed carbon electrode ink is capable of this when formulated with an orthogonal solvent system. This innovative layer can be applied continuously and compatibly with the underlying layers at a low temperature and high speed.”
The carbon ink was specifically formulated for compatibility with the perovskite material and the slot die coating process by combining conductive carbon particles, polymer binder, and solvent. The combination of polymer and solvent was carefully controlled so that the ink could flow through the coating head to produce continuous electrodes, which are formed when the solvent evaporates leaving the conductive carbon bound together by the polymer binder.
“The biggest challenge was compatibility of materials and compatibility of process,” noted Beynon. “Perovskite is easily degraded by incompatible solvents. Therefore a solvent system for our ink had to be compatible with not only the perovskite active layer but also the sandwiching semiconductors. This solvent and conductive carbon ink system also had to be compatible with the slot die coating system, tailored to have a rheology compatible with narrow channels and process window of slot die coating.”
The final result was an R2R system that printed large volumes of flexible, rollable perovskite solar cells that exited the printing press, ready to generate power. Testing showed these cells produced a stabilized PCE of 10.8 percent (close to the 13 percent to 14 percent PCE range for cells printed using the conventional but more problematic gold electrode method).
Even with a pilot lab-scale printing set-up, the production rate was 115 times higher than that for conventional perovskite solar cells.
Remarkable stability
What surprised Beynon the most was the stability of the devices. “The lifetime of a perovskite solar cell is a critical concern and was not something we were considering as part of this research,” he explained. “It was a surprise to find that our device structure and printed carbon electrodes improved the stability of the perovskite cells, compared to gold with no encapsulation of the devices.” However, one of the factors driving perovskite degradation is moisture and the carbon electrodes are hydrophobic, effectively providing protection to the active material and thereby increasing the lifetime.
The most exciting aspect of demonstrating entirely roll-to-roll coated perovskite solar cells for the first time is that the success and further improvements to come will be driven by engineering.
“Using large-scale printing equipment is highly dependent upon controlling the process parameters, from the interaction between coating speed and pump flow rate to the use of low flow limit to predict and then control the stable coating window,” he said. “We must continuously print defect-free films as thin as 50 nm—something that is impossible without control and optimization of the substrate handling such as tension control and web guiding of the polyethylene terephthalate (PET) substrate.”
Moving forward
Beynon and his team are working to improve all layers of the device stack, including replacing the perovskite material with the higher-performing multi-cation perovskite materials. This will hopefully lead to higher conversion efficiencies that could approach the typical 17 percent conversion efficiency of domestic solar panels in use today.
The flexibility of these new perovskite solar panels could make them ideal for surfaces that previously could not accept solar cells, such as curved surfaces, roofs, facades, and polytunnels.
“We have achieved printing perovskite solar cells where we feed a plastic substrate into the printing press and take working solar cells out,” said Beynon. “This provides us with a platform that we will use to improve the performance of the cells by changing the device layers, introducing interlayers, and employing higher-performing perovskite chemistry.
“We are also looking forward to producing prototype panels that can be deployed for outdoor testing, demonstrating that these perovskite modules can be used in a real-world environment to generate electricity at low cost.”
Mark Crawford is a technology writer in Corrales, N.M.
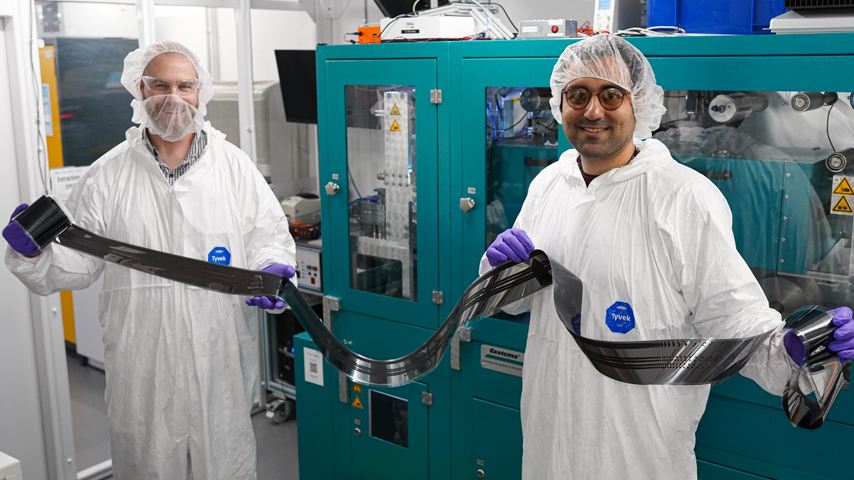
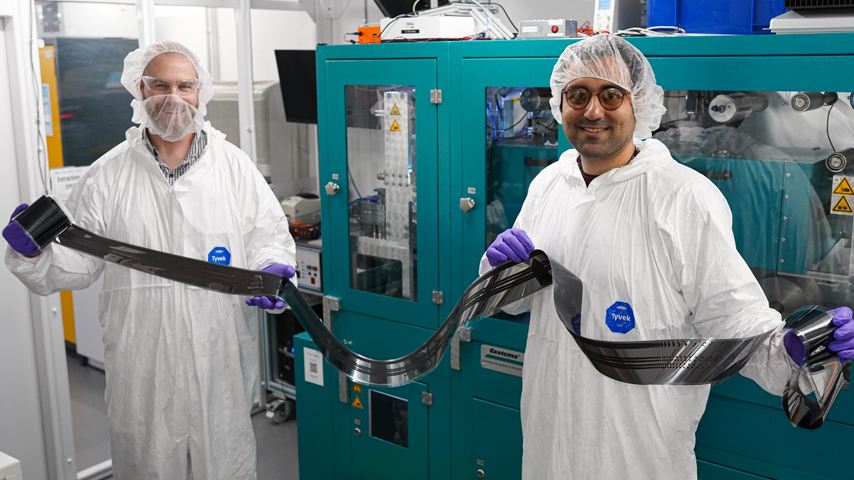