Bright Fortunes Await the Gas Turbine Industry
Bright Fortunes Await the Gas Turbine Industry
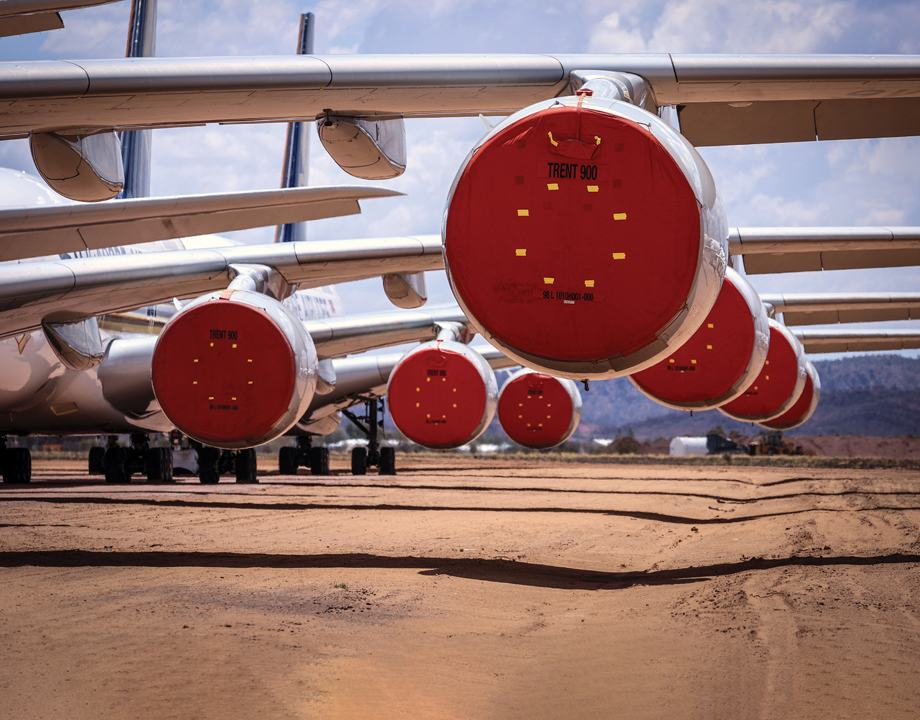
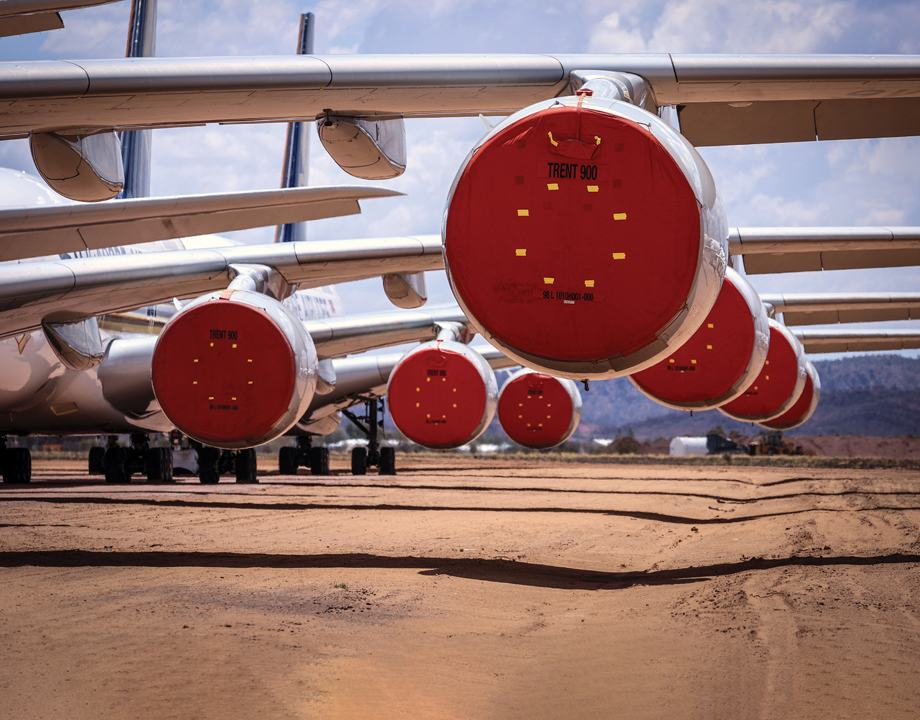
Make no mistake: 2020 was a bad year for the gas turbine industry. Pandemic-idled aircraft around the world may be forced to be retired from service. Photo: David Gray/Bloomberg via Getty Images
The heart of my annual review of the gas turbine industry—the first of which appeared in this magazine in 2000—is a checkup on the value of all the gas turbines produced in the previous year. Most years, it’s good news as the industry grows and more people recognize the virtues of these remarkable machines. Even when one market sector declines, other markets are ready to take up the slack.
I don’t think I’ll be spoiling the rest of the article by revealing that 2020 was not one of those years. The total industry declined. The civilian aviation market declined, and the military aviation market declined. The electric power generation market declined, and the mechanical drive market declined. It was a grim year all around the world, as the COVID-19 pandemic killed millions and cratered economies. The gas turbine industry reflects that adversity.
This is not the first upheaval the industry has faced. The technology was born on the cusp of catastrophe: Both the aviation and nonaviation versions of the gas turbine were perfected and demonstrated in 1939, as the world was rushing toward the start of the Second World War. In those dark months and the disastrous ones that followed, no one could have guessed that gas turbines would become ubiquitous in aviation and record-setting in the electric power industry.
The current crisis is nothing like the one that started in 1939. By the time you read this, a majority of Americans—and a growing number of people from around the world—will have had the opportunity to be vaccinated against the pandemic-producing coronavirus, and the global economy should begin recovering some of its lost ground.
The gas turbine industry, which had been growing before the pandemic, ought to begin to regain some of its former momentum. Also, much of the way that gas turbines were only a footnote to a momentous 1939, there are some promising advances in the technology that don’t contribute much at the moment, but which may improve the fortunes of the industry—and all of us—in the coming decades.
When I want to get a full sense of the entire market, I turn to Forecast International, a market research firm in Newtown, CT. As part of its operations, FI provides a financial picture of the worldwide gas turbine industry, its history, current state, and forecasted future.
Using computer models and an extensive database, FI’s staff has computed the value of worldwide gas turbine manufacturing production from 1990 to 2020 and has predicted values to 2034—encompassing 44 of the 95 years of gas turbine history by that point. FI reports that the value of production (which the company considers being more accurate than reported sales) for all gas turbines worldwide for 2020 was $54 billion, down from $87.1 billion in 2018, a 38 percent drop, due to the 2019-2020 start of the COVID-19 pandemic. FI predicts that this will return to $88.4 billion in 2023 with growth to $115.5 billion in 2031, 10 years after that.
More by Lee S. Langston: Hits and Errors for the Gas Turbine Industry
Aside from a short period at the beginning of the 2000s, the aviation market, which serves both civilian and military aircraft, makes up more than 80 percent of the gas turbine market. In 2020, the value of production for the aviation market was $44.6 billion, down from $74.7 billion in 2018. That decline was entirely due to reduced production in the civilian aviation market, which dropped from $66.3 billion in 2018 to just $35.7 billion in 2020, a two-year decline of 46 percent.
This sudden chasm in jet engine production has been like no other in commercial aviation history. As the pandemic ebbs, the public will resume air travel, but the trajectory of recovery for the jet engine industry projects to be shallow. There will be a lag in new commercial jet engine orders as the airlines cash in on “green-time” assets.
Roughly about half the global airline fleet has been grounded by the pandemic—about 14,000 commercial aircraft. To cut costs while the travel industry was essentially mothballed, airlines have retired a portion of these parked jet airliners, which frees up “green-time” engines: engines that still have service life remaining. Having such engines on hand, which can be swapped into operating aircraft when their engines exit their scheduled service life, enables airlines to defer costly engine restorations to a later date. The net result will be to postpone further profitable original equipment manufacturers (OEM) engine parts and new engine sales for some period, even after worldwide airline flights recover.
Also, hurt are OEM business models of selling “power by the hour” (instead of the engines themselves) or offering engines at near-zero cost and making up their value in engine maintenance visits and spare parts sales.
The military market value of production last year was $8.9 billion and has been essentially flat since 2015. In a normal year, the military market is one-sixth or one-seventh of the commercial market and produces far fewer (though more expensive) engines. For instance, the largest worldwide military jet engine program at the moment is the engine for the Lockheed Martin Joint Strike Fighter F-35; since 2009, just over 750 Pratt & Whitney 40,000 lbf F135s have been delivered. But the market segment’s influence is much more significant than its production value. Advanced military jet engine technology, from engine efficiency improvements to long-life single crystal turbine blades, has historically migrated to other types of gas turbines.
The nonaviation market did not see quite as large a pandemic-induced hit to production value, though it did fall 25 percent to $9.4 billion in 2020 from $12.5 billion in 2018. The components of the nonaviation market are mechanical drive at $1.5 billion, marine at $0.7 billion, and electrical power at $7.2 billion. There are interconnections between these markets: Gas turbine power plants are fueled mostly by pipeline natural gas, whose pressures and flow rates are maintained by compression stations (about one every 100 kilometers), with compressors that in turn are powered by mechanical drive gas turbines, which also burn natural gas. And the marine market caters to large ships that use gas turbines to drive auxiliary power units for their extensive electrical systems.
The electric power market for gas turbines has seen a couple of booms and busts over the past 30 years. During the 2001 peak, when irrationally exuberant energy investors overreacted to electric utility deregulation and created an oversupply of gas turbine power plants, their value of production reached $32 billion in inflation-adjusted dollars, briefly eclipsing the aviation market. The market collapsed to just $8 million in 2003, then rose again to around $20 billion in 2009 and 2010 before drifting to about half that before the pandemic.
In spite of that inconstant demand, gas turbines have become a dominant means of electrical power production in the United States, accounting for about 40 percent of electric generation in 2019, and are growing in prominence around the world. Because of their design, gas turbines have a number of advantages over steam power: They are compact, require less start-up time to reach peak output operation, have a lower initial cost, and produce large amounts of power considering their weight and size.
In the 1990s, gas turbine combustors and hot turbine technology advanced so that in electric power gas turbines, exhaust gas exit temperatures reached 1,000 °F (538 °C). These exhaust gases were hot enough to pass through a heat recovery steam generator (HRSG) and drive a steam turbine, generating more electrical power. By combining a gas turbine (a Brayton cycle heat engine) and a steam turbine (a Rankine cycle heat engine) in a single power plant, these two prime movers generate electrical power using one unit of fuel, with one thermodynamic cycle feeding the other.
More about the Gas Turbine Industry: Engineers Find New Uses for Gas Turbines
These combined cycle gas turbine plants offer many of the same advantages as simple cycle gas turbine plants. They have low capital costs, ranging between $700 and $1,000 per kilowatt, compared to $3,000 per kilowatt for coal and $6,000 (or more) per kilowatt for nuclear. And because combined cycle gas turbine plants can rapidly start-up and shut down as needed, they can provide reliable backup power for emergencies and intermittent renewable power facilities.
Access to inexpensive natural gas from shale deposits has spurred many generating asset operators to switch from coal-fired Rankine cycle plants. Simply swapping the fuel source from coal to gas will yield some gains in terms of carbon emissions, but even gas-fired Rankine-cycle power plants emit more carbon dioxide per unit of electricity produced than do combined-cycle plants. An illustration of the potential saving is found at the Lake Charles Power Station in Westlake, La., which began commercial operation in March 2020; It is expected to emit 40 percent fewer CO₂ than the previous, older gas-fired steam-power plant it replaced.
But one of the most significant advantages is that combining these two cycles into one power-generation operation yields greater thermal efficiency. Using conservation of energy and the definition of thermodynamic thermal efficiency, the combined cycle thermal efficiency can be derived fairly simply as the sum of the two cycles’ efficiencies minus their product. Operating alone, the thermal efficiencies of the Brayton and Rankine cycles can be estimated to be about 40 percent (a good value for modern gas turbines) and 30 percent (a reasonable value at typical conditions), respectively.
Together in a combined cycle gas turbine plant, they achieve an estimated average of 58 percent thermal efficiency, a remarkable increase. The best-in-class combined-cycle plants can do even better, approaching thermal efficiencies as high as 65 percent—double that of most existing single cycle coal-fired plants. With power outputs greater than 1,000 megawatts, they are the most efficient heat engines yet designed by humankind.
Often, when technology reaches a pinnacle as the gas turbine has with its dominance in the aircraft propulsion and its records in fuel efficiency, it would be natural to assume it has approached a point of maturity where the only remaining advances are incremental. That isn’t the case here. There are a couple of technological frontiers that could help reshape the gas turbine industry in the coming decades.
One of these is adapting turbines to burn hydrogen as fuel. Hydrogen has a long history with gas turbines—in 1937, the very first testbed German jet engine used hydrogen because of its high flame speed, wide combustion limits, and gaseous state. As we know, that pathway wasn’t pursued, since all the advantages of hydrogen, including its specific heat value (highest of any fuel and three times that of jet fuel) and its nonpolluting exhaust, are counterbalanced by the absence of readily available free hydrogen. As a highly reactive element, it must be separated from its reactants, which exacts an energy penalty.
Currently, most of the hydrogen used commercially comes from the steam reforming of coal or natural gas, which creates a carbon dioxide byproduct that energy companies are desperate to avoid. However, hydrogen can also be obtained from the electrolysis of water—using electricity to split water into oxygen and hydrogen. If the electrical power used for electrolysis is obtained from renewables, such as wind or solar, it can rightly be called “green hydrogen.”
As many nations pursue wind, solar, geothermal, biomass, and other renewables, it becomes more likely that green, emission-free hydrogen—created from a surplus of renewable energy—will be available to integrate into energy production. Companies and countries are currently researching hydrogen injection into gas pipelines and networks already in use by power plants, and a number of pilot programs are in progress.
More on Hydrogen: Hydrogen Evolution or Revolution?
Southern California Gas Company is field-testing, injecting green hydrogen blends (from 1 percent to 20 percent) into its gas pipelines, and utilities in the United Kingdom are blending hydrogen (up to 20 percent in one use) to fuel power plants. And more efficient, environmentally friendly “hydrogen-ready” plants are already in development. The Long Ridge Energy Terminal, a 485-MW plant being built along the Ohio River and scheduled to begin production in fall 2021, will use a blend of natural gas and 5 percent hydrogen, with the goal of using 100 percent hydrogen by 2030. The other advance worth keeping an eye on is in closed cycle configurations that use supercritical carbon dioxide (sCO₂) as the working fluid.
Under atmospheric conditions, carbon dioxide ice doesn’t melt but instead sublimates, turning directly into vapor. Under high enough pressure and temperature—above 72.8 atmospheres and 31 °C—the gas becomes a supercritical fluid, taking on some properties of both liquid and gas and exhibiting an unusually good solvent. For instance, supercritical CO₂ is employed in the coffee industry as a decaffeination agent. If used as a working fluid in a gas turbine, it promises increased power density, reduced compressor work, and increased thermal efficiency at lower turbine temperatures.
The ever-adaptable gas turbine is currently being studied, tested, and developed by various groups and organizations to use sCO₂ as a working fluid in high-efficiency, closed-cycle configurations. One design study by Sandia National Laboratories for a 100-MW supercritical CO₂ Brayton cycle power plant shows that it could have a thermal efficiency of 50 percent. That compares favorably to the similarly sized General Electric LMS100, which holds the record for the highest efficiency simple cycle gas turbine plant, 44.7 percent.
If a Brayton cycle sCO₂ gas turbine could be successfully run at 50 percent, it’s worth speculating what would happen if it replaced the Rankine cycle in a combined-cycle gas turbine plant. The resulting plant thermal efficiency (with the air gas turbine at 40 percent) might be as high as a record-setting 70 percent.
At present, a combined-cycle plant yokes together the Brayton cycle and a Rankine cycle. Perhaps the cycles to be combined in the future will both be Brayton cycles, one that’s open and one that’s closed. Not only would that provide greater efficiency and—if powered by green hydrogen—reduced environmental impact, but it would also increase the numbers of gas turbines sold. Even in a year with so much trouble, there is potential for bright fortunes ahead for the gas turbine industry.
Lee S. Langston is professor emeritus of mechanical engineering at the University of Connecticut in Storrs and a frequent contributor to Mechanical Engineering.
I don’t think I’ll be spoiling the rest of the article by revealing that 2020 was not one of those years. The total industry declined. The civilian aviation market declined, and the military aviation market declined. The electric power generation market declined, and the mechanical drive market declined. It was a grim year all around the world, as the COVID-19 pandemic killed millions and cratered economies. The gas turbine industry reflects that adversity.
This is not the first upheaval the industry has faced. The technology was born on the cusp of catastrophe: Both the aviation and nonaviation versions of the gas turbine were perfected and demonstrated in 1939, as the world was rushing toward the start of the Second World War. In those dark months and the disastrous ones that followed, no one could have guessed that gas turbines would become ubiquitous in aviation and record-setting in the electric power industry.
The current crisis is nothing like the one that started in 1939. By the time you read this, a majority of Americans—and a growing number of people from around the world—will have had the opportunity to be vaccinated against the pandemic-producing coronavirus, and the global economy should begin recovering some of its lost ground.
The gas turbine industry, which had been growing before the pandemic, ought to begin to regain some of its former momentum. Also, much of the way that gas turbines were only a footnote to a momentous 1939, there are some promising advances in the technology that don’t contribute much at the moment, but which may improve the fortunes of the industry—and all of us—in the coming decades.
Green Time Blues
When I want to get a full sense of the entire market, I turn to Forecast International, a market research firm in Newtown, CT. As part of its operations, FI provides a financial picture of the worldwide gas turbine industry, its history, current state, and forecasted future.
Using computer models and an extensive database, FI’s staff has computed the value of worldwide gas turbine manufacturing production from 1990 to 2020 and has predicted values to 2034—encompassing 44 of the 95 years of gas turbine history by that point. FI reports that the value of production (which the company considers being more accurate than reported sales) for all gas turbines worldwide for 2020 was $54 billion, down from $87.1 billion in 2018, a 38 percent drop, due to the 2019-2020 start of the COVID-19 pandemic. FI predicts that this will return to $88.4 billion in 2023 with growth to $115.5 billion in 2031, 10 years after that.
More by Lee S. Langston: Hits and Errors for the Gas Turbine Industry
Aside from a short period at the beginning of the 2000s, the aviation market, which serves both civilian and military aircraft, makes up more than 80 percent of the gas turbine market. In 2020, the value of production for the aviation market was $44.6 billion, down from $74.7 billion in 2018. That decline was entirely due to reduced production in the civilian aviation market, which dropped from $66.3 billion in 2018 to just $35.7 billion in 2020, a two-year decline of 46 percent.
This sudden chasm in jet engine production has been like no other in commercial aviation history. As the pandemic ebbs, the public will resume air travel, but the trajectory of recovery for the jet engine industry projects to be shallow. There will be a lag in new commercial jet engine orders as the airlines cash in on “green-time” assets.
Roughly about half the global airline fleet has been grounded by the pandemic—about 14,000 commercial aircraft. To cut costs while the travel industry was essentially mothballed, airlines have retired a portion of these parked jet airliners, which frees up “green-time” engines: engines that still have service life remaining. Having such engines on hand, which can be swapped into operating aircraft when their engines exit their scheduled service life, enables airlines to defer costly engine restorations to a later date. The net result will be to postpone further profitable original equipment manufacturers (OEM) engine parts and new engine sales for some period, even after worldwide airline flights recover.
Also, hurt are OEM business models of selling “power by the hour” (instead of the engines themselves) or offering engines at near-zero cost and making up their value in engine maintenance visits and spare parts sales.
The military market value of production last year was $8.9 billion and has been essentially flat since 2015. In a normal year, the military market is one-sixth or one-seventh of the commercial market and produces far fewer (though more expensive) engines. For instance, the largest worldwide military jet engine program at the moment is the engine for the Lockheed Martin Joint Strike Fighter F-35; since 2009, just over 750 Pratt & Whitney 40,000 lbf F135s have been delivered. But the market segment’s influence is much more significant than its production value. Advanced military jet engine technology, from engine efficiency improvements to long-life single crystal turbine blades, has historically migrated to other types of gas turbines.
Boom and Bust
The nonaviation market did not see quite as large a pandemic-induced hit to production value, though it did fall 25 percent to $9.4 billion in 2020 from $12.5 billion in 2018. The components of the nonaviation market are mechanical drive at $1.5 billion, marine at $0.7 billion, and electrical power at $7.2 billion. There are interconnections between these markets: Gas turbine power plants are fueled mostly by pipeline natural gas, whose pressures and flow rates are maintained by compression stations (about one every 100 kilometers), with compressors that in turn are powered by mechanical drive gas turbines, which also burn natural gas. And the marine market caters to large ships that use gas turbines to drive auxiliary power units for their extensive electrical systems.
The electric power market for gas turbines has seen a couple of booms and busts over the past 30 years. During the 2001 peak, when irrationally exuberant energy investors overreacted to electric utility deregulation and created an oversupply of gas turbine power plants, their value of production reached $32 billion in inflation-adjusted dollars, briefly eclipsing the aviation market. The market collapsed to just $8 million in 2003, then rose again to around $20 billion in 2009 and 2010 before drifting to about half that before the pandemic.
In spite of that inconstant demand, gas turbines have become a dominant means of electrical power production in the United States, accounting for about 40 percent of electric generation in 2019, and are growing in prominence around the world. Because of their design, gas turbines have a number of advantages over steam power: They are compact, require less start-up time to reach peak output operation, have a lower initial cost, and produce large amounts of power considering their weight and size.
In the 1990s, gas turbine combustors and hot turbine technology advanced so that in electric power gas turbines, exhaust gas exit temperatures reached 1,000 °F (538 °C). These exhaust gases were hot enough to pass through a heat recovery steam generator (HRSG) and drive a steam turbine, generating more electrical power. By combining a gas turbine (a Brayton cycle heat engine) and a steam turbine (a Rankine cycle heat engine) in a single power plant, these two prime movers generate electrical power using one unit of fuel, with one thermodynamic cycle feeding the other.
More about the Gas Turbine Industry: Engineers Find New Uses for Gas Turbines
These combined cycle gas turbine plants offer many of the same advantages as simple cycle gas turbine plants. They have low capital costs, ranging between $700 and $1,000 per kilowatt, compared to $3,000 per kilowatt for coal and $6,000 (or more) per kilowatt for nuclear. And because combined cycle gas turbine plants can rapidly start-up and shut down as needed, they can provide reliable backup power for emergencies and intermittent renewable power facilities.
Access to inexpensive natural gas from shale deposits has spurred many generating asset operators to switch from coal-fired Rankine cycle plants. Simply swapping the fuel source from coal to gas will yield some gains in terms of carbon emissions, but even gas-fired Rankine-cycle power plants emit more carbon dioxide per unit of electricity produced than do combined-cycle plants. An illustration of the potential saving is found at the Lake Charles Power Station in Westlake, La., which began commercial operation in March 2020; It is expected to emit 40 percent fewer CO₂ than the previous, older gas-fired steam-power plant it replaced.
But one of the most significant advantages is that combining these two cycles into one power-generation operation yields greater thermal efficiency. Using conservation of energy and the definition of thermodynamic thermal efficiency, the combined cycle thermal efficiency can be derived fairly simply as the sum of the two cycles’ efficiencies minus their product. Operating alone, the thermal efficiencies of the Brayton and Rankine cycles can be estimated to be about 40 percent (a good value for modern gas turbines) and 30 percent (a reasonable value at typical conditions), respectively.
Together in a combined cycle gas turbine plant, they achieve an estimated average of 58 percent thermal efficiency, a remarkable increase. The best-in-class combined-cycle plants can do even better, approaching thermal efficiencies as high as 65 percent—double that of most existing single cycle coal-fired plants. With power outputs greater than 1,000 megawatts, they are the most efficient heat engines yet designed by humankind.
On the Horizon
Often, when technology reaches a pinnacle as the gas turbine has with its dominance in the aircraft propulsion and its records in fuel efficiency, it would be natural to assume it has approached a point of maturity where the only remaining advances are incremental. That isn’t the case here. There are a couple of technological frontiers that could help reshape the gas turbine industry in the coming decades.
One of these is adapting turbines to burn hydrogen as fuel. Hydrogen has a long history with gas turbines—in 1937, the very first testbed German jet engine used hydrogen because of its high flame speed, wide combustion limits, and gaseous state. As we know, that pathway wasn’t pursued, since all the advantages of hydrogen, including its specific heat value (highest of any fuel and three times that of jet fuel) and its nonpolluting exhaust, are counterbalanced by the absence of readily available free hydrogen. As a highly reactive element, it must be separated from its reactants, which exacts an energy penalty.
Currently, most of the hydrogen used commercially comes from the steam reforming of coal or natural gas, which creates a carbon dioxide byproduct that energy companies are desperate to avoid. However, hydrogen can also be obtained from the electrolysis of water—using electricity to split water into oxygen and hydrogen. If the electrical power used for electrolysis is obtained from renewables, such as wind or solar, it can rightly be called “green hydrogen.”
As many nations pursue wind, solar, geothermal, biomass, and other renewables, it becomes more likely that green, emission-free hydrogen—created from a surplus of renewable energy—will be available to integrate into energy production. Companies and countries are currently researching hydrogen injection into gas pipelines and networks already in use by power plants, and a number of pilot programs are in progress.
More on Hydrogen: Hydrogen Evolution or Revolution?
Southern California Gas Company is field-testing, injecting green hydrogen blends (from 1 percent to 20 percent) into its gas pipelines, and utilities in the United Kingdom are blending hydrogen (up to 20 percent in one use) to fuel power plants. And more efficient, environmentally friendly “hydrogen-ready” plants are already in development. The Long Ridge Energy Terminal, a 485-MW plant being built along the Ohio River and scheduled to begin production in fall 2021, will use a blend of natural gas and 5 percent hydrogen, with the goal of using 100 percent hydrogen by 2030. The other advance worth keeping an eye on is in closed cycle configurations that use supercritical carbon dioxide (sCO₂) as the working fluid.
Under atmospheric conditions, carbon dioxide ice doesn’t melt but instead sublimates, turning directly into vapor. Under high enough pressure and temperature—above 72.8 atmospheres and 31 °C—the gas becomes a supercritical fluid, taking on some properties of both liquid and gas and exhibiting an unusually good solvent. For instance, supercritical CO₂ is employed in the coffee industry as a decaffeination agent. If used as a working fluid in a gas turbine, it promises increased power density, reduced compressor work, and increased thermal efficiency at lower turbine temperatures.
The ever-adaptable gas turbine is currently being studied, tested, and developed by various groups and organizations to use sCO₂ as a working fluid in high-efficiency, closed-cycle configurations. One design study by Sandia National Laboratories for a 100-MW supercritical CO₂ Brayton cycle power plant shows that it could have a thermal efficiency of 50 percent. That compares favorably to the similarly sized General Electric LMS100, which holds the record for the highest efficiency simple cycle gas turbine plant, 44.7 percent.
If a Brayton cycle sCO₂ gas turbine could be successfully run at 50 percent, it’s worth speculating what would happen if it replaced the Rankine cycle in a combined-cycle gas turbine plant. The resulting plant thermal efficiency (with the air gas turbine at 40 percent) might be as high as a record-setting 70 percent.
At present, a combined-cycle plant yokes together the Brayton cycle and a Rankine cycle. Perhaps the cycles to be combined in the future will both be Brayton cycles, one that’s open and one that’s closed. Not only would that provide greater efficiency and—if powered by green hydrogen—reduced environmental impact, but it would also increase the numbers of gas turbines sold. Even in a year with so much trouble, there is potential for bright fortunes ahead for the gas turbine industry.
Lee S. Langston is professor emeritus of mechanical engineering at the University of Connecticut in Storrs and a frequent contributor to Mechanical Engineering.
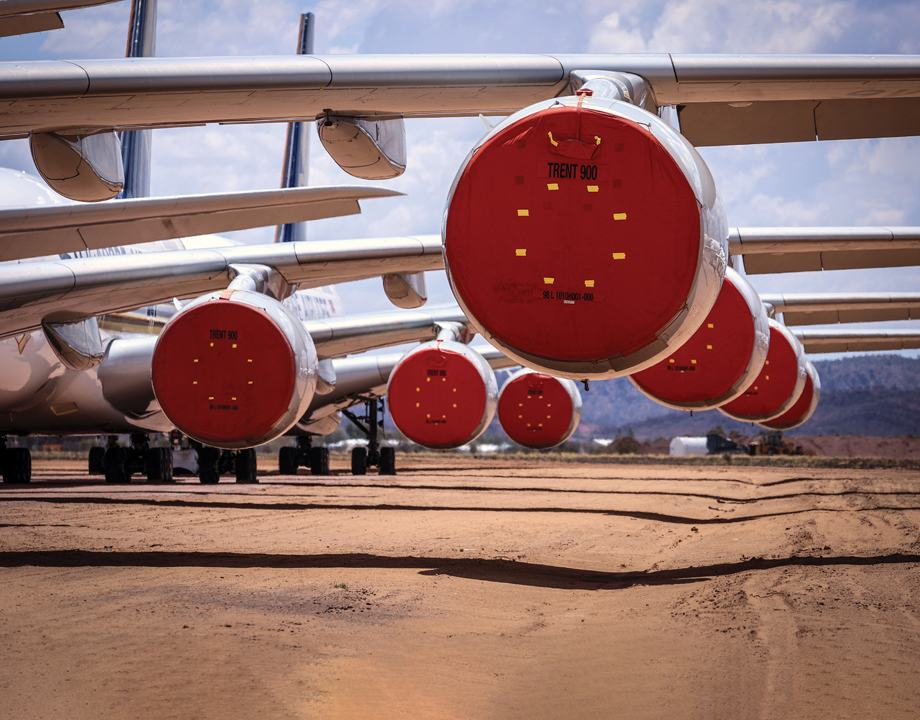
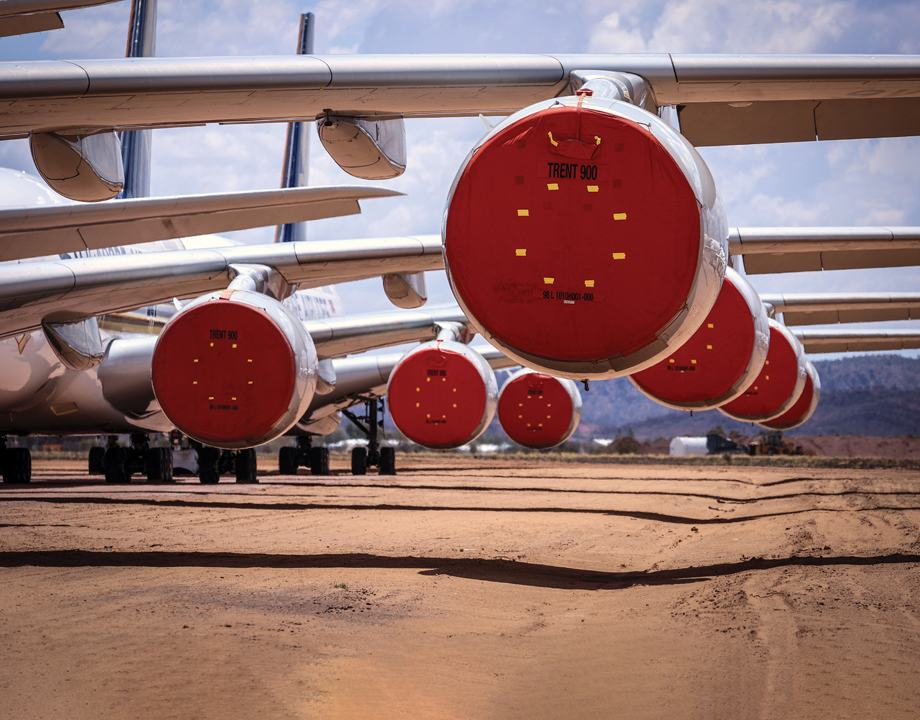