Hits and Errors for Gas Turbine Industry
Hits and Errors for Gas Turbine Industry
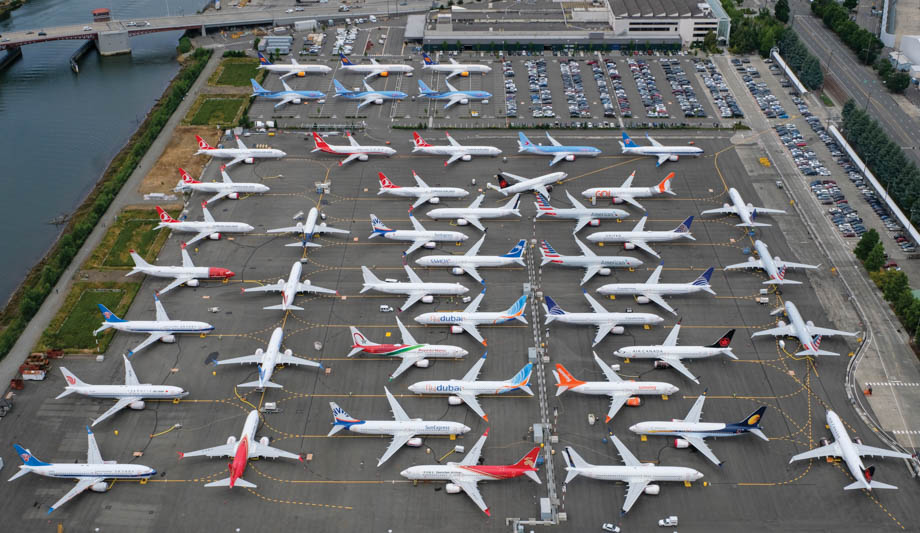
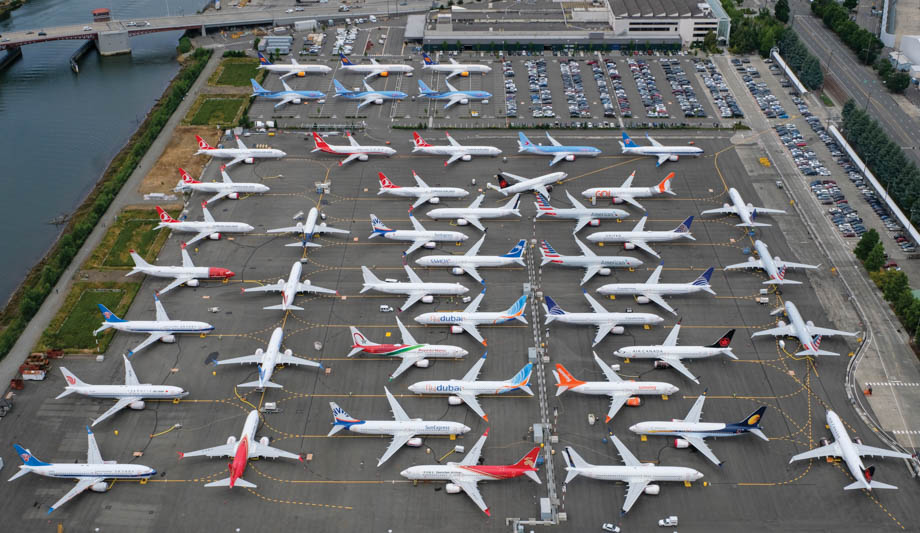
Dozens of new Boeing 737 MAX airplanes sit idle in a lot adjacent to Boeing Field. The fleet has been grounded by aviation agencies since March 2019. Photo by Stephen Brashear/Getty Images
Nobody likes mistakes, nor does anyone like to own up to them. We’re familiar with the bloodless, corporate construction, “Mistakes were made.” And the famous, “Victory has 100 fathers and defeat is an orphan.”
The gas turbine industry has had many successes, but this past year it has been dogged by the specter of two great mistakes—one that occurred, and another than is being threatened. The one that is obvious to anyone who read a newspaper or watched the news was the design flaw in Boeing’s 737 MAX 8, which led to two horrific accidents and the grounding of the entire fleet. That mistake is still rippling through the commercial aircraft industry and the gas turbine manufacturing companies that build jet engines.
The other mistake hasn’t yet happened, and might be averted, but it is even more serious than the faulty engine configuration on the 737 MAX 8. Many groups are pushing for the immediate elimination of natural gas as a fuel source, and some jurisdictions have begun to ban new residential gas hook-ups. It has been stated in some quarters that using natural gas for electric power generation is no better than burning coal, and that gas turbine power plants ought to be closed.
This action would be an enormous mistake. It would, of course, create a crisis for a major segment of the gas turbine industry. But more importantly, it would close down one of the most important tools we have on hand to bring down power sector carbon emissions, and it would threaten the development of a new, zero-emissions electric generating system before it has a chance to prove itself.
The mistakes found in the 737 MAX 8 have already been made and need to be repaired. The turning away from natural gas power can be avoided. But will it?
Gas turbines have found uses in a wide variety of applications. They are used in mechanical drives that compress natural gas and move it along continent-spanning pipelines. They are found on large ships to provide auxiliary power. Modest-sized gas turbines form the heart of innovative combined heat and power systems. It is a clean, efficient, and flexible technology that is well suited to modern needs.
To get a full sense of the nearly $90-billion market, each year I turn to Forecast International (FI). FI is a market research firm in Newtown, Conn., which provides a financial picture of the worldwide gas turbine industry, its history, current state, and forecasted future. Using computer models and an extensive data base, FI’s Stuart Slade has computed the value of worldwide gas turbine manufacturing production from 1990 to 2019, and has predicted values to 2033. (FI considers production figures to be more accurate than reported sales.)
Slade reports that the value of production for all gas turbines worldwide for 2019 was $87.2 billion, up from $84.7 billion in 2018. FI predicts that by 2033, production will reach $114.9 billion, representing a 32 percent growth in 14 years.
Based on FI’s value of production history and predictions, the worldwide gas turbine industry is and will be a global energy converter industry for the foreseeable future. The forecast is, as always, a snapshot based on the state of various industries and the world economy as of the first months of 2020.
In 2019 the value of production for non-aviation was $10.8 billion or about 12 percent of the total market. Production of mechanical drive gas turbines, usually installed to drive compressors in liquefied natural gas plants and to boost pressure along natural gas pipelines, amounted to $1.7 billion for 2019; while marine gas turbines, used to drive shipboard generators for propulsion and electricity, accounted for $530 million.
Those two segments were swamped by the value of production of gas turbines for electric generation. Currently, these gas turbines range in outputs from 30 kW (Capstone Turbine) to 567 MW (Siemens), with thermal efficiencies as high as 44 percent. The dominant fuel is natural gas, with the ability to switch to fuel oil in many cases. The total value of production for the electric generation segment was $8.6 billion in 2019. This level is still far less than the $31.8 billion inflation adjusted value of production in 2001 when investors overreacted to electric utility deregulation and rushed to purchase gas turbines. Mistakes were made.
You May Also Like: Engineering Ways to Improve Electrical Grid Resilience
The aviation side of the market is far bigger, but that bland statement undersells exactly what drives the gas turbine industry. The aviation market is split into military and civilian segments, and the military is quite high profile. That market benefits from the performance improvements that filter down from technology originating from military operational needs. Although relatively small numbers of military jet engines are sold each year, they account for a value of production of some $9.7 billion in 2019—larger than the electric generation market and nearly equal to the entire non-aviation segment.
Yet even that healthy market is overshadowed by the colossus of the civilian aviation market. The value of production of gas turbines for commercial aircraft was $76.4 billion in 2019 and FI forecasts that the market will continue to climb to $97.6 billion in 2033. Those current values and projections are a function of the financial health of the airline industry. When business is good, the natural tendency is to expand. Larger fleets made of newer planes lead inexorably to new orders for jet engines.
Airline jets come in two basic classes. The largest and more prestigious is designated by its interior configuration: Twin-aisle, wide-body or TAWB. Although TAWBs such as Boeing’s 747 and 787 and Airbus’s A340 and A380 are physically larger and more expensive, the market for commercial aircraft is actually dominated by smaller, shorter-range aircraft. That class is also referred to by its interior configuration—single-aisle, narrow-body, or SANB—and is the most lucrative market for both airframe and engine companies.
The SANB market has been dominated for decades by two main workhorses. Boeing’s 737 had its first flight 1967 and Airbus followed with its A320, which had its first flight in 1987. The two families are roughly equivalent, and each can be powered by twin 20,000-30,000 pounds-thrust (lbt) engines from one of two international consortiums: CMF International and International Aero Engines. So popular and profitable have these aircraft been that in 2011, Boeing estimated the SANB market for the next twenty years would be a remarkable $2 trillion.
That forecast was thrown into doubt last year due to apparent design flaws in Boeing’s latest series of 737s. Boeing’s segment of the SANB market is experiencing OEM setbacks not seen since the hull-loss crashes of the de Havilland Comet jets in the early 1950s.
The Boeing crisis has its origin with successful gas turbines, of all things. A new generation of fuel efficient turbofan engines, especially the Pratt & Whitney geared fan engines and the LEAP engines from CFM International (a consortium of GE Aviation and Safran Aircraft Engines), have revolutionized the economics of SANB aircraft. The new engines provided a fuel savings of between 15 and 20 percent, which can either increase the aircraft range (adding the possibility of more routes for shorter-range aircraft) or significantly reduce fuel costs on existing routes. The result was a clamor for re-engined SANB aircraft from airline customers.
Boeing chose the CFMI LEAP engine to replace the previous CFMI CFM-56-7, for its new 737 line, called 737 MAX. The potential fuel savings were considerable, but the LEAP engine was considerably larger than its predecessor—a 69.4-inch fan versus a 60-inch fan. That meant that to provide enough ground clearance, the LEAP engine nacelle had to be mounted slightly higher and farther forward on the wing.
Recommended for You: The Engineer Who Discovered Global Warming
Each new fix brought up new challenges. The repositioning of the larger nacelle changed the flight dynamics. The nacelle body actually provided lift at high angles of attack, such as during a climb. And since the LEAP nacelle is ahead of the plane’s center of gravity, this uncontrolled nacelle lift causes a slight pitch-up effect, which, if sustained, would bring the aircraft closer to stall, and a devastating loss of aircraft lift.
Instead of employing physical aerodynamic fixes for this uncontrolled LEAP nacelle lift, Boeing engineers relied on software. They created an automated anti-stall system, called MCAS, that expands how the 737 MAX horizontal stabilizer is automatically adjusted to counter the uncontrolled nacelle lift. This flight control software depends on a sensed angle of attack from a fuselage-mounted probe.
This was a mistake. Malfunction of the probe combined with MCAS system flaws led to the two 737 MAX fatal crashes, which together claimed 346 lives. The two crashes within a span of six months (and less than two years after the plane had been certified) led to the entire 737 MAX fleet to be grounded in March 2019. At press time, that fleet—387 aircraft across 59 airlines around the globe—was still grounded.
This past January, Boeing estimated their total costs to the airframe company brought about by the grounding may come to about $19 billion. These dire events have not only presented a major financial hit for Boeing, but it has inflicted reputational harm to an airframe company that was long revered for its successful aviation history.
Hopefully, Boeing engineers (and perhaps a new enlightened management) will come up with software and hardware solutions, so that the 737 MAX avoids the fate of the 1950s Comet 1 jet aircraft, which after a series of hull losses was permanently pulled from service. And that the company avoids the fate of de Havilland, which never recovered from the debacle and was later sold and folded.
The mistakes made by Boeing can’t be undone at this point, only mitigated. But there is another potential mistake looming that could affect not only the gas turbine industry, but the health of the planet. Fortunately, there is time to avert it.
Many segments of society, such as student bodies at U.S. universities (including mine at the University of Connecticut), are apprehensive about global warming and advocate for the immediate elimination of the use of carbon-containing fossil fuels. They have been targeting coal and oil companies, but have also placed the use of natural gas in the crosshairs. Several municipalities are banning new residential gas hook-ups and some activists have started to refer to methane as being as bad as coal in terms of its climate impact.
Such words and actions are certainly heartfelt, but they also display a lack of awareness of the recent showstopper reduction of CO2 emissions by the use of natural gas fueled gas turbines. To quote Harvard cognitive scientist and author Steven Pinker, “To get an accurate picture of the world, you have to count.”
Since 2005, natural gas fired gas turbines have contributed to a major reduction in carbon dioxide emissions from power plants in the United States. For example, in 2018, which had a same level of total annual net electric generation as 2005, CO2 power plant emissions in the U.S. dropped by 27 percent from 2005. This amounted to a 2018 annual reduction of 647 million metric tons (Mmt)—nearly equal to the total CO2 2017 emissions of Germany, the world’s fourth largest economy—a remarkable emissions reduction fact not widely recognized.
According to data from the U.S. Energy Information Administration, the 647 Mmt reduction was brought about by the retirement of 853 billion kWh of coal-fired Rankine cycle power plants, and replaced by 257 billion kWh of intermittent wind turbine power and 682 billion kWh of dispatchable natural gas power plants (whose fuel has half the carbon content of coal). Thus, Rankine cycle coal-fired power plants (at about 30 percent thermal efficiency) were replaced by natural gas-fired gas turbines combined cycle electric power plants, with record breaking thermal efficiencies of as high as 60-64 percent. The combined effects of halving the fuel’s carbon content and the higher record-breaking gas turbine combined cycle efficiency, cuts carbon emissions per unit of electricity by potentially as much as 75 percent.
This is not the 100 percent reduction in carbon emissions exhorted by some activists, but using Pinker’s admonition “to count,” gas turbine use burning natural gas provides an enlightened view of sensible and substantial CO2 reduction.
The EIA reports that in 2019 the share of coal used as a fuel for electric power generation had fallen to 23.5 percent in the U.S. Coal fueled more than half of electric generation for a generation starting around 1980 and cleared that level as recently as 2008, at the time of the Financial Crisis. At the global level, coal is still the dominant fuel, accounting for 38 percent of electric power generation. The worldwide availability of natural gas is being enhanced by fracking, new pipeline construction (such as Russia’s Gasprom Nord Stream 2 to Germany) and its transportation as LNG. Thus gas turbine combined cycle plants could easily be used to significantly lower CO2 emissions in other parts of the world, as has been done in the U.S.
Read Our Energy Blog: The Oil Industry is Part of the Solution
It would be a mistake to turn away from natural gas at this point, as building new gas-powered gas turbines to replace coal-fired plants is the quickest route to lower carbon emissions. Eliminating gas would also make it harder to develop what might be the best means of achieving practical zero-emissions power.
Recently, gas turbine manufacturers such as Ansaldo Energia, Mitsubishi, Kawasaki, and Siemens have investigated operating these machines with hydrogen, either pure or mixed with natural gas to decarbonize gas turbine exhaust products. The attraction is obvious: Pure hydrogen combustion would produce water vapor emissions, rather than CO2. It should be noted that hydrogen was used as the fuel for Hans von Ohain’s very first test jet engine, in Germany, in 1937.
Efforts in Japan extend beyond the turbomachinery to such issues as the hydrogen energy supply chain. A consortium of Japanese manufacturers has partnered with AGL, a leading energy firm in Australia, on a pilot project, called HySTRA, to turn brown coal from a mine 100 miles east of Melbourne into liquefied hydrogen. The first liquefied hydrogen tanker was launched in December 2019, and is expected to deliver its first shipment of hydrogen to Kobe by the end of this year. The process would still produce CO2, which would need to be sequestered to be a carbon-neutral process.
European groups have begun to explore hydrogen for use in gas turbine electric power plants, but using surplus electrical power from wind turbines and solar power units instead of coal to electrolyze water. The electrolytic-produced hydrogen could either be stored or injected into natural gas pipeline systems.
These efforts show great promise for creating a zero-emissions power system that could support renewable and nuclear power. Indeed, hydrogen-burning gas turbines promise a flexibility and efficiency that could be a real game-changer in clean power. But the prospects for hydrogen depend on their being able to build off of existing natural gas infrastructure; it would be prohibitively costly to reinvent the pipelines and storage facilities.
Gas has been great on its own terms in bringing down carbon emissions. And by providing a bridge to a hydrogen-fuel paradigm, it could help eliminate emissions altogether. Abandoning gas now would be a colossal mistake.
Lee S. Langston is professor emeritus of mechanical engineering at the University of Connecticut in Storrs and a frequent contributor to Mechanical Engineering.
The gas turbine industry has had many successes, but this past year it has been dogged by the specter of two great mistakes—one that occurred, and another than is being threatened. The one that is obvious to anyone who read a newspaper or watched the news was the design flaw in Boeing’s 737 MAX 8, which led to two horrific accidents and the grounding of the entire fleet. That mistake is still rippling through the commercial aircraft industry and the gas turbine manufacturing companies that build jet engines.
The other mistake hasn’t yet happened, and might be averted, but it is even more serious than the faulty engine configuration on the 737 MAX 8. Many groups are pushing for the immediate elimination of natural gas as a fuel source, and some jurisdictions have begun to ban new residential gas hook-ups. It has been stated in some quarters that using natural gas for electric power generation is no better than burning coal, and that gas turbine power plants ought to be closed.
This action would be an enormous mistake. It would, of course, create a crisis for a major segment of the gas turbine industry. But more importantly, it would close down one of the most important tools we have on hand to bring down power sector carbon emissions, and it would threaten the development of a new, zero-emissions electric generating system before it has a chance to prove itself.
The mistakes found in the 737 MAX 8 have already been made and need to be repaired. The turning away from natural gas power can be avoided. But will it?
$90-Billion Market
Gas turbines have found uses in a wide variety of applications. They are used in mechanical drives that compress natural gas and move it along continent-spanning pipelines. They are found on large ships to provide auxiliary power. Modest-sized gas turbines form the heart of innovative combined heat and power systems. It is a clean, efficient, and flexible technology that is well suited to modern needs.
To get a full sense of the nearly $90-billion market, each year I turn to Forecast International (FI). FI is a market research firm in Newtown, Conn., which provides a financial picture of the worldwide gas turbine industry, its history, current state, and forecasted future. Using computer models and an extensive data base, FI’s Stuart Slade has computed the value of worldwide gas turbine manufacturing production from 1990 to 2019, and has predicted values to 2033. (FI considers production figures to be more accurate than reported sales.)
Slade reports that the value of production for all gas turbines worldwide for 2019 was $87.2 billion, up from $84.7 billion in 2018. FI predicts that by 2033, production will reach $114.9 billion, representing a 32 percent growth in 14 years.
Based on FI’s value of production history and predictions, the worldwide gas turbine industry is and will be a global energy converter industry for the foreseeable future. The forecast is, as always, a snapshot based on the state of various industries and the world economy as of the first months of 2020.
In 2019 the value of production for non-aviation was $10.8 billion or about 12 percent of the total market. Production of mechanical drive gas turbines, usually installed to drive compressors in liquefied natural gas plants and to boost pressure along natural gas pipelines, amounted to $1.7 billion for 2019; while marine gas turbines, used to drive shipboard generators for propulsion and electricity, accounted for $530 million.
Those two segments were swamped by the value of production of gas turbines for electric generation. Currently, these gas turbines range in outputs from 30 kW (Capstone Turbine) to 567 MW (Siemens), with thermal efficiencies as high as 44 percent. The dominant fuel is natural gas, with the ability to switch to fuel oil in many cases. The total value of production for the electric generation segment was $8.6 billion in 2019. This level is still far less than the $31.8 billion inflation adjusted value of production in 2001 when investors overreacted to electric utility deregulation and rushed to purchase gas turbines. Mistakes were made.
You May Also Like: Engineering Ways to Improve Electrical Grid Resilience
The aviation side of the market is far bigger, but that bland statement undersells exactly what drives the gas turbine industry. The aviation market is split into military and civilian segments, and the military is quite high profile. That market benefits from the performance improvements that filter down from technology originating from military operational needs. Although relatively small numbers of military jet engines are sold each year, they account for a value of production of some $9.7 billion in 2019—larger than the electric generation market and nearly equal to the entire non-aviation segment.
Yet even that healthy market is overshadowed by the colossus of the civilian aviation market. The value of production of gas turbines for commercial aircraft was $76.4 billion in 2019 and FI forecasts that the market will continue to climb to $97.6 billion in 2033. Those current values and projections are a function of the financial health of the airline industry. When business is good, the natural tendency is to expand. Larger fleets made of newer planes lead inexorably to new orders for jet engines.
Airline jets come in two basic classes. The largest and more prestigious is designated by its interior configuration: Twin-aisle, wide-body or TAWB. Although TAWBs such as Boeing’s 747 and 787 and Airbus’s A340 and A380 are physically larger and more expensive, the market for commercial aircraft is actually dominated by smaller, shorter-range aircraft. That class is also referred to by its interior configuration—single-aisle, narrow-body, or SANB—and is the most lucrative market for both airframe and engine companies.
The SANB market has been dominated for decades by two main workhorses. Boeing’s 737 had its first flight 1967 and Airbus followed with its A320, which had its first flight in 1987. The two families are roughly equivalent, and each can be powered by twin 20,000-30,000 pounds-thrust (lbt) engines from one of two international consortiums: CMF International and International Aero Engines. So popular and profitable have these aircraft been that in 2011, Boeing estimated the SANB market for the next twenty years would be a remarkable $2 trillion.
That forecast was thrown into doubt last year due to apparent design flaws in Boeing’s latest series of 737s. Boeing’s segment of the SANB market is experiencing OEM setbacks not seen since the hull-loss crashes of the de Havilland Comet jets in the early 1950s.
A New Challenge
The Boeing crisis has its origin with successful gas turbines, of all things. A new generation of fuel efficient turbofan engines, especially the Pratt & Whitney geared fan engines and the LEAP engines from CFM International (a consortium of GE Aviation and Safran Aircraft Engines), have revolutionized the economics of SANB aircraft. The new engines provided a fuel savings of between 15 and 20 percent, which can either increase the aircraft range (adding the possibility of more routes for shorter-range aircraft) or significantly reduce fuel costs on existing routes. The result was a clamor for re-engined SANB aircraft from airline customers.
Boeing chose the CFMI LEAP engine to replace the previous CFMI CFM-56-7, for its new 737 line, called 737 MAX. The potential fuel savings were considerable, but the LEAP engine was considerably larger than its predecessor—a 69.4-inch fan versus a 60-inch fan. That meant that to provide enough ground clearance, the LEAP engine nacelle had to be mounted slightly higher and farther forward on the wing.
Recommended for You: The Engineer Who Discovered Global Warming
Each new fix brought up new challenges. The repositioning of the larger nacelle changed the flight dynamics. The nacelle body actually provided lift at high angles of attack, such as during a climb. And since the LEAP nacelle is ahead of the plane’s center of gravity, this uncontrolled nacelle lift causes a slight pitch-up effect, which, if sustained, would bring the aircraft closer to stall, and a devastating loss of aircraft lift.
Instead of employing physical aerodynamic fixes for this uncontrolled LEAP nacelle lift, Boeing engineers relied on software. They created an automated anti-stall system, called MCAS, that expands how the 737 MAX horizontal stabilizer is automatically adjusted to counter the uncontrolled nacelle lift. This flight control software depends on a sensed angle of attack from a fuselage-mounted probe.
This was a mistake. Malfunction of the probe combined with MCAS system flaws led to the two 737 MAX fatal crashes, which together claimed 346 lives. The two crashes within a span of six months (and less than two years after the plane had been certified) led to the entire 737 MAX fleet to be grounded in March 2019. At press time, that fleet—387 aircraft across 59 airlines around the globe—was still grounded.
This past January, Boeing estimated their total costs to the airframe company brought about by the grounding may come to about $19 billion. These dire events have not only presented a major financial hit for Boeing, but it has inflicted reputational harm to an airframe company that was long revered for its successful aviation history.
Hopefully, Boeing engineers (and perhaps a new enlightened management) will come up with software and hardware solutions, so that the 737 MAX avoids the fate of the 1950s Comet 1 jet aircraft, which after a series of hull losses was permanently pulled from service. And that the company avoids the fate of de Havilland, which never recovered from the debacle and was later sold and folded.
A Carbon Solution
The mistakes made by Boeing can’t be undone at this point, only mitigated. But there is another potential mistake looming that could affect not only the gas turbine industry, but the health of the planet. Fortunately, there is time to avert it.
Many segments of society, such as student bodies at U.S. universities (including mine at the University of Connecticut), are apprehensive about global warming and advocate for the immediate elimination of the use of carbon-containing fossil fuels. They have been targeting coal and oil companies, but have also placed the use of natural gas in the crosshairs. Several municipalities are banning new residential gas hook-ups and some activists have started to refer to methane as being as bad as coal in terms of its climate impact.
Such words and actions are certainly heartfelt, but they also display a lack of awareness of the recent showstopper reduction of CO2 emissions by the use of natural gas fueled gas turbines. To quote Harvard cognitive scientist and author Steven Pinker, “To get an accurate picture of the world, you have to count.”
Since 2005, natural gas fired gas turbines have contributed to a major reduction in carbon dioxide emissions from power plants in the United States. For example, in 2018, which had a same level of total annual net electric generation as 2005, CO2 power plant emissions in the U.S. dropped by 27 percent from 2005. This amounted to a 2018 annual reduction of 647 million metric tons (Mmt)—nearly equal to the total CO2 2017 emissions of Germany, the world’s fourth largest economy—a remarkable emissions reduction fact not widely recognized.
According to data from the U.S. Energy Information Administration, the 647 Mmt reduction was brought about by the retirement of 853 billion kWh of coal-fired Rankine cycle power plants, and replaced by 257 billion kWh of intermittent wind turbine power and 682 billion kWh of dispatchable natural gas power plants (whose fuel has half the carbon content of coal). Thus, Rankine cycle coal-fired power plants (at about 30 percent thermal efficiency) were replaced by natural gas-fired gas turbines combined cycle electric power plants, with record breaking thermal efficiencies of as high as 60-64 percent. The combined effects of halving the fuel’s carbon content and the higher record-breaking gas turbine combined cycle efficiency, cuts carbon emissions per unit of electricity by potentially as much as 75 percent.
This is not the 100 percent reduction in carbon emissions exhorted by some activists, but using Pinker’s admonition “to count,” gas turbine use burning natural gas provides an enlightened view of sensible and substantial CO2 reduction.
The EIA reports that in 2019 the share of coal used as a fuel for electric power generation had fallen to 23.5 percent in the U.S. Coal fueled more than half of electric generation for a generation starting around 1980 and cleared that level as recently as 2008, at the time of the Financial Crisis. At the global level, coal is still the dominant fuel, accounting for 38 percent of electric power generation. The worldwide availability of natural gas is being enhanced by fracking, new pipeline construction (such as Russia’s Gasprom Nord Stream 2 to Germany) and its transportation as LNG. Thus gas turbine combined cycle plants could easily be used to significantly lower CO2 emissions in other parts of the world, as has been done in the U.S.
Read Our Energy Blog: The Oil Industry is Part of the Solution
It would be a mistake to turn away from natural gas at this point, as building new gas-powered gas turbines to replace coal-fired plants is the quickest route to lower carbon emissions. Eliminating gas would also make it harder to develop what might be the best means of achieving practical zero-emissions power.
Recently, gas turbine manufacturers such as Ansaldo Energia, Mitsubishi, Kawasaki, and Siemens have investigated operating these machines with hydrogen, either pure or mixed with natural gas to decarbonize gas turbine exhaust products. The attraction is obvious: Pure hydrogen combustion would produce water vapor emissions, rather than CO2. It should be noted that hydrogen was used as the fuel for Hans von Ohain’s very first test jet engine, in Germany, in 1937.
Efforts in Japan extend beyond the turbomachinery to such issues as the hydrogen energy supply chain. A consortium of Japanese manufacturers has partnered with AGL, a leading energy firm in Australia, on a pilot project, called HySTRA, to turn brown coal from a mine 100 miles east of Melbourne into liquefied hydrogen. The first liquefied hydrogen tanker was launched in December 2019, and is expected to deliver its first shipment of hydrogen to Kobe by the end of this year. The process would still produce CO2, which would need to be sequestered to be a carbon-neutral process.
European groups have begun to explore hydrogen for use in gas turbine electric power plants, but using surplus electrical power from wind turbines and solar power units instead of coal to electrolyze water. The electrolytic-produced hydrogen could either be stored or injected into natural gas pipeline systems.
These efforts show great promise for creating a zero-emissions power system that could support renewable and nuclear power. Indeed, hydrogen-burning gas turbines promise a flexibility and efficiency that could be a real game-changer in clean power. But the prospects for hydrogen depend on their being able to build off of existing natural gas infrastructure; it would be prohibitively costly to reinvent the pipelines and storage facilities.
Gas has been great on its own terms in bringing down carbon emissions. And by providing a bridge to a hydrogen-fuel paradigm, it could help eliminate emissions altogether. Abandoning gas now would be a colossal mistake.
Lee S. Langston is professor emeritus of mechanical engineering at the University of Connecticut in Storrs and a frequent contributor to Mechanical Engineering.
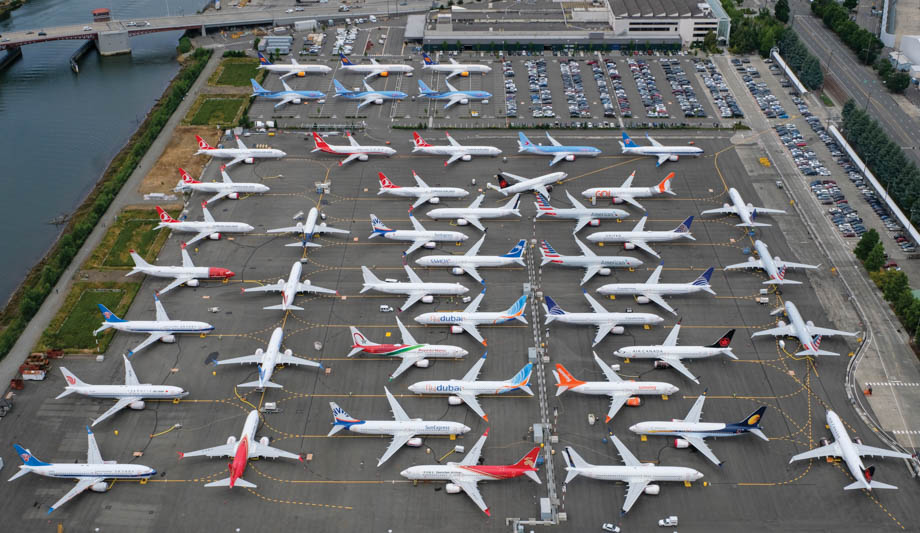
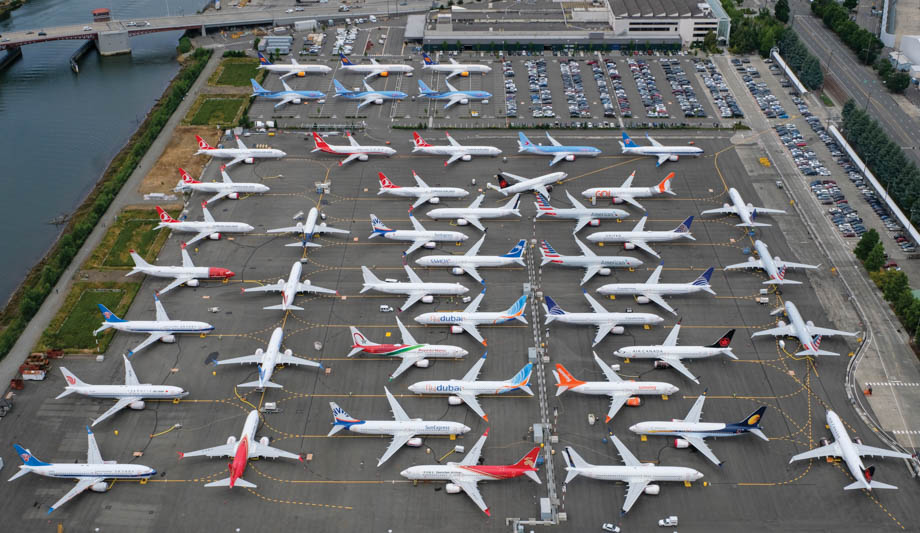