Smart Coatings on Implants Transmit Health Data in Real Time
Smart Coatings on Implants Transmit Health Data in Real Time
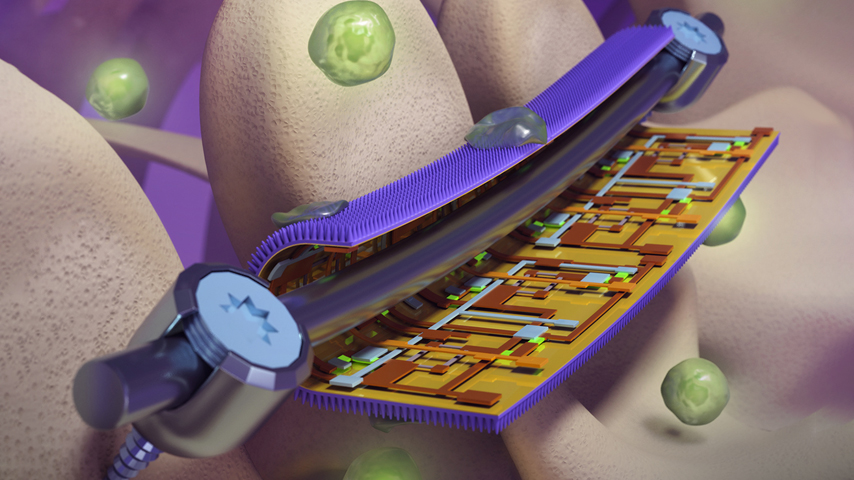
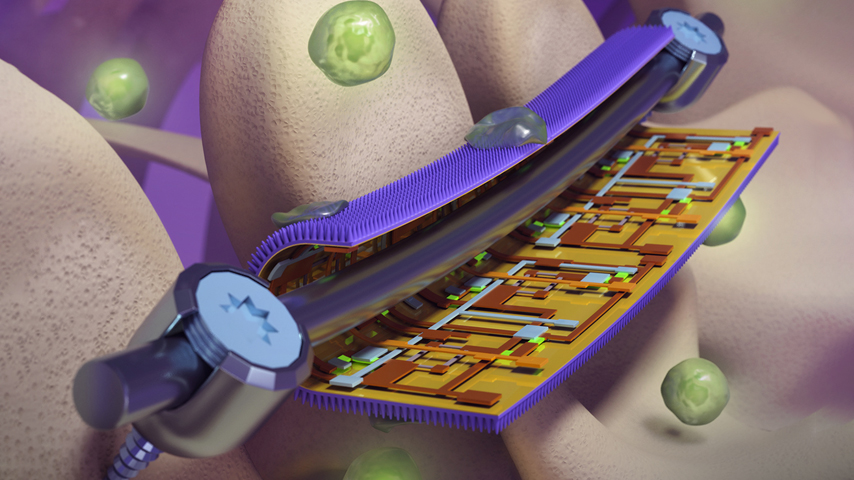
A foil coating with nanostructures for orthopedic implants virtually eliminates bacterial growth and can detect when implants are starting to fail.
Infection and device failures are major problems with orthopedic implants, affecting up to 10 percent of patients. Dangerous biofilms can still form on water-repellant materials and antimicrobial coatings can run out in a few months, leading to toxic effects on healthy surrounding tissue. Device failures can include loosening or mechanical issues with function and/or fit, which can also reflect poor bone in-growth.
To improve this situation, researchers at the University of Illinois, Urbana-Champaign have developed a “smart” coating for surgical orthopedic implants that can monitor strain on the devices to provide early warning of implant failures, while also killing infection-causing bacteria. Early detection of implant malfunction can lead to quicker intervention to help treat the condition before it becomes a larger problem.
“I was fascinated by this idea,” said Cao. “Being a material scientist, my natural instinct told me that I could probably build something using man-made soft materials—perhaps with enhanced performance and more functions—that could do better than Mother Nature.”
You Might Also Enjoy: Image Capturing Device Mimics the Human Eye
Inspired by the naturally antibacterial wings of cicadas and dragonflies, Cao and his team created an ultrathin foil patterned with nanoscale pillars like those found on the insects' wings. When a bacterial cell attempts to bind to the foil, the pillars puncture the cell wall and kill it. To add even more functionality, on the back side of the nanostructured foil, where it comes into contact with the implant device, the team integrated arrays of highly sensitive, flexible electronic sensors to monitor strain.
The researchers then teamed up with veterinary clinical medicine professor Annette McCoy to test their prototype devices. They implanted the foils in live mice and monitored them for any sign of infection, even when bacteria were introduced. They also applied the coatings to commercially available spinal implants and monitored strain to the implants in sheep spines under normal load for device failure diagnosis.
Cao was pleasantly surprised by how well the prototypes performed for both functions. The nanopillars showed they can kill more than 99 percent of different strains of pathogenic bacteria without the use of chemicals. For measuring strain, tiny stress changes down to 0.1 percent were precisely measured, which could serve as a potential way to reliably detect different physiological conditions during the healing progress for orthopedic surgeries.
One of the biggest challenges, Cao noted, was working across the disciplinary boundaries to develop this technology. Tasks ranged from preparing the templates with nanoscale high aspect ratio features, optimizing the micro-molding of polymers, and integrating with flexible electronic strain sensors, all the way to validating the performance and functionalities in both in vitro and in vivo models.
“Our work required expertise on microfabrication, chemistry, materials science, electrical engineering, mechanical engineering, cell biology, pathobiology, and medical sciences,” he said. “That is also what made this research so exciting—it was the result of collaboration among seven research groups at the University of Illinois Urbana Champaign. I would especially like to acknowledge the contribution from professor Yumeng Li, the mechanical engineer on our team.”
Become a Member: How to Join ASME
Several aspects of Cao’s research should interest mechanical engineers. First, there is the critical mechanical design challenge of achieving the high killing efficacy with high-aspect ratio pillars, while still maintaining the structural robustness of these nanostructures. Second, on the other side of the foil, Cao integrated flexible strain sensors built on ultrathin silicon nanomembrane.
“From the mechanical engineering perspective, we reduced the thickness of single crystalline silicon down to about 100 nm,” said Cao. “This allowed it to be flexible enough to be conformally applied on the curved surfaces of orthopedic implants, but still maintain its excellent piezoelectric properties as a single crystalline semiconductor, which is critical for ensuring the high gauge factor, another mechanical engineering trick.”
The coatings integrate flexible sensors with a nanostructured antibacterial surface. The prototype electronics required wires. In the next stage of research, the team hopes to develop wireless power and data communications interfaces for their coatings—a crucial step for clinical application. They are also working to develop large-scale production of the nanopillar-textured bacteria-killing foil.
“We are trying to scale up the fabrication of bioinspired mechano-bactericidal foils and further verify the performance/functionality of the dual functional smart coating foils with large animal models,” Cao said. “We are also building a start-up company to further develop these ideas and commercialize this technology.”
Mark Crawford is technology writer in Corrales, N.M.
To improve this situation, researchers at the University of Illinois, Urbana-Champaign have developed a “smart” coating for surgical orthopedic implants that can monitor strain on the devices to provide early warning of implant failures, while also killing infection-causing bacteria. Early detection of implant malfunction can lead to quicker intervention to help treat the condition before it becomes a larger problem.
Inspired by nature
A few years ago, lead researcher Qing Cao, professor of materials science and engineering at the University of Illinois, was intrigued by a paper he had read that revealed how cicada wings can kill bacteria through physical/mechanical interactions.“I was fascinated by this idea,” said Cao. “Being a material scientist, my natural instinct told me that I could probably build something using man-made soft materials—perhaps with enhanced performance and more functions—that could do better than Mother Nature.”
You Might Also Enjoy: Image Capturing Device Mimics the Human Eye
Inspired by the naturally antibacterial wings of cicadas and dragonflies, Cao and his team created an ultrathin foil patterned with nanoscale pillars like those found on the insects' wings. When a bacterial cell attempts to bind to the foil, the pillars puncture the cell wall and kill it. To add even more functionality, on the back side of the nanostructured foil, where it comes into contact with the implant device, the team integrated arrays of highly sensitive, flexible electronic sensors to monitor strain.
The researchers then teamed up with veterinary clinical medicine professor Annette McCoy to test their prototype devices. They implanted the foils in live mice and monitored them for any sign of infection, even when bacteria were introduced. They also applied the coatings to commercially available spinal implants and monitored strain to the implants in sheep spines under normal load for device failure diagnosis.
Cao was pleasantly surprised by how well the prototypes performed for both functions. The nanopillars showed they can kill more than 99 percent of different strains of pathogenic bacteria without the use of chemicals. For measuring strain, tiny stress changes down to 0.1 percent were precisely measured, which could serve as a potential way to reliably detect different physiological conditions during the healing progress for orthopedic surgeries.
One of the biggest challenges, Cao noted, was working across the disciplinary boundaries to develop this technology. Tasks ranged from preparing the templates with nanoscale high aspect ratio features, optimizing the micro-molding of polymers, and integrating with flexible electronic strain sensors, all the way to validating the performance and functionalities in both in vitro and in vivo models.
“Our work required expertise on microfabrication, chemistry, materials science, electrical engineering, mechanical engineering, cell biology, pathobiology, and medical sciences,” he said. “That is also what made this research so exciting—it was the result of collaboration among seven research groups at the University of Illinois Urbana Champaign. I would especially like to acknowledge the contribution from professor Yumeng Li, the mechanical engineer on our team.”
Become a Member: How to Join ASME
Several aspects of Cao’s research should interest mechanical engineers. First, there is the critical mechanical design challenge of achieving the high killing efficacy with high-aspect ratio pillars, while still maintaining the structural robustness of these nanostructures. Second, on the other side of the foil, Cao integrated flexible strain sensors built on ultrathin silicon nanomembrane.
“From the mechanical engineering perspective, we reduced the thickness of single crystalline silicon down to about 100 nm,” said Cao. “This allowed it to be flexible enough to be conformally applied on the curved surfaces of orthopedic implants, but still maintain its excellent piezoelectric properties as a single crystalline semiconductor, which is critical for ensuring the high gauge factor, another mechanical engineering trick.”
Expanding scope and scale
Much of Cao’s research involved combining biomimetic physical antimicrobial nanostructures with flexible strain mapping electronics in a single device design, with the hope of solving a critical biomedical challenge regarding orthopedic implants. Innovative mechanical engineering designs were essential for achieving both the anti-infection and diagnostic functionalities.The coatings integrate flexible sensors with a nanostructured antibacterial surface. The prototype electronics required wires. In the next stage of research, the team hopes to develop wireless power and data communications interfaces for their coatings—a crucial step for clinical application. They are also working to develop large-scale production of the nanopillar-textured bacteria-killing foil.
“We are trying to scale up the fabrication of bioinspired mechano-bactericidal foils and further verify the performance/functionality of the dual functional smart coating foils with large animal models,” Cao said. “We are also building a start-up company to further develop these ideas and commercialize this technology.”
Mark Crawford is technology writer in Corrales, N.M.
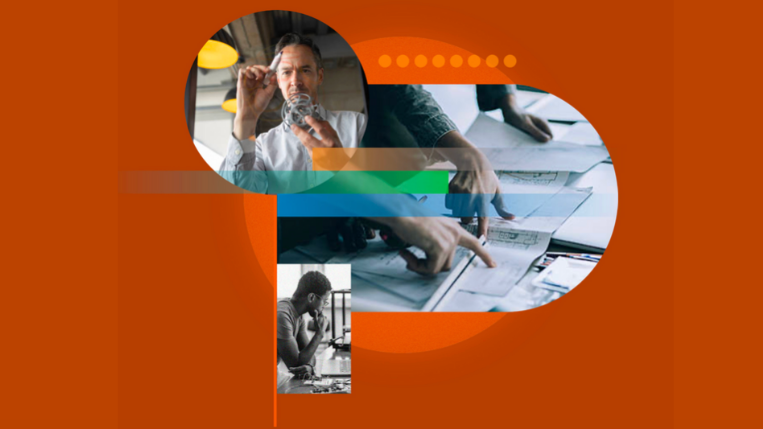
Pulse of the Profession: Design for Manufacturing
The walls between design and manufacturing have been steadily coming down, with new technologies and ways of working giving engineers full visibility into production processes and constraints.
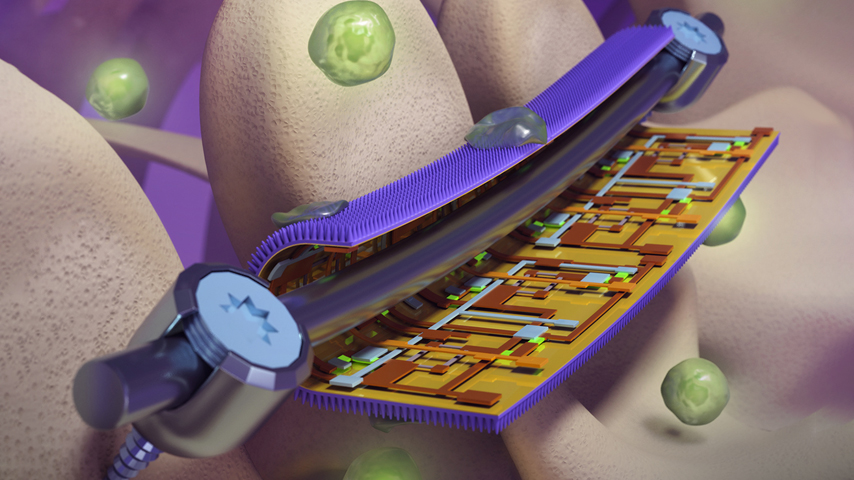
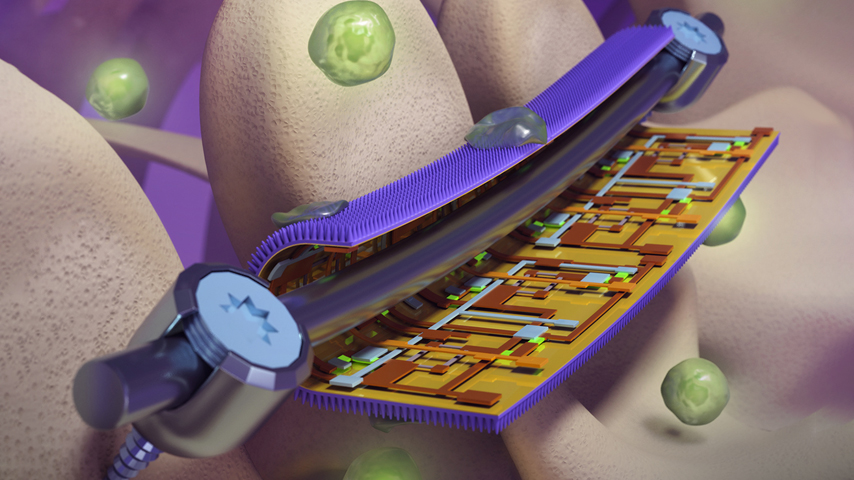