Porous Structures Give Metamaterial Key Properties
Porous Structures Give Metamaterial Key Properties
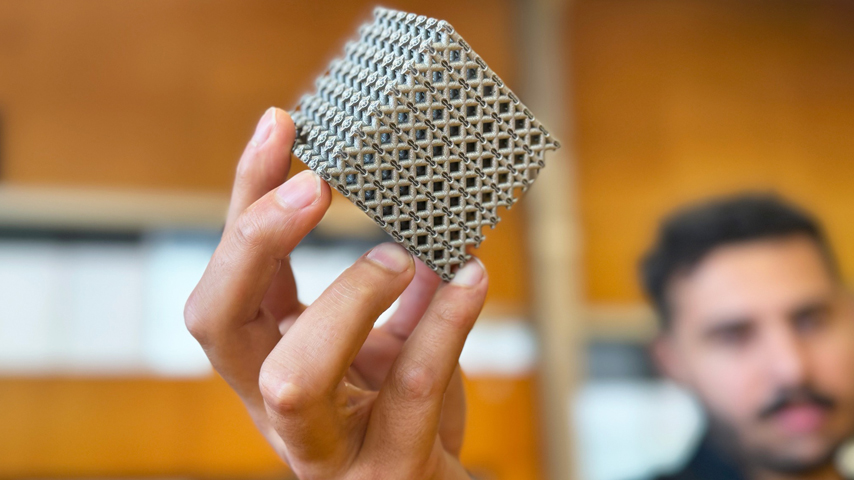
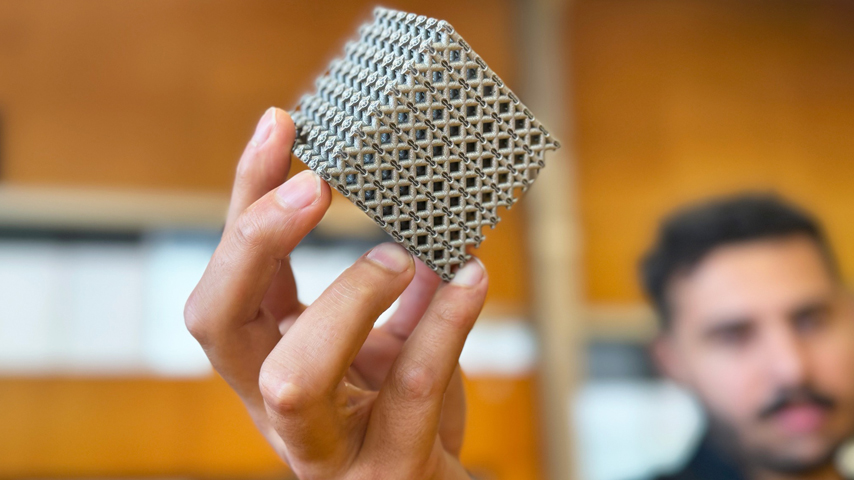
A combination of two types of lattices helps make this printed titanium material lightweight, heat-resistant, and strong.
At first glance, much of the natural environment looks solid through and through. However, beneath the surface, many natural materials hold pores and intricate internal structures that enhance their robustness and resistance to various types of failures when subject to stress and abuse. Plant structures feature pores called stoma that aid in the absorption of water and sunlight while minimizing the weight the plants must self-support. Sandstone exhibits interconnected pores, facilitating the passage of water. Human bones contain a porous center housing bone marrow, allowing for the passage of cells and nutrients.
Inspired by nature’s sophisticated designs, researchers at the Royal Melbourne Institute of Technology (RMIT) in Australia have combined two types of lattice structures to create a metamaterial they printed in titanium. The metamaterial boasts high strength, lightweight properties, corrosion resistance, and high-temperature durability. The researchers also found that it was capable of uniformly distributing stress, reducing deformation, and enhancing strength.
Engineers have for decades attempted to produce materials that mimic the combination of strength and airiness found in natural materials. Two types of repeating lattice structures that have been tested are hollow strut lattices (HSL) and thin plate lattices (TPL). But neither proved to have been successful. HSLs utilize interconnected channels to distribute forces throughout the structure while maintaining a lightweight design. Despite this, they fail to evenly distribute forces, resulting in failure points where the channels intersect. Conversely, TPLs employ interconnected thin plates in a lattice configuration to evenly distribute stress, albeit with solid plates.
A metamaterial is a type of composite where the properties arise from its engineered structure, rather than the bulk materials it is made of. The material engineered by the RMIT researchers combines the HSLs and TPLs into a metamaterial that negates the weaknesses of each type of lattice. The metamaterial is capable of uniformly distributing stress, reducing deformation, and providing unparalleled strength.
According to Ma Qian, a distinguished professor of advanced manufacturing and materials at RMIT, “The more uniform the distribution of the stress throughout the structure, the better the performance of the structure. Our design has a reasonably uniform distribution of stress; therefore, the performance improves a lot.”
Such a complicated structure could not be manufactured using conventional manufacturing methods. Instead, the researchers relied on laser powder bed fusion, an additive manufacturing process that prints 3D parts in layers using metal powder and a laser beam, essentially drawing the part in a series of stacked 2D layers. This process not only enabled intricate and non-uniform designs but also permitted the removal of excess, unfused powder from the part after printing, creating a porous network within the part.
“3D metal printing has offered unprecedented design and manufacturing abilities for us to create new metallic materials for various purposes,” Qian said.
Researchers crafted the metamaterial using titanium alloy Ti-6Al-4V, known for its corrosion resistance, especially in marine or seawater environments, high strength, and heat resistance up to 350 °C (662 °F). This alloy is often used in critical applications, notably aerospace and biomechanics for implants and prostheses. Additionally, the RMIT team proposed that if the metamaterial is printed from another titanium alloy, Ti-SF61, it would offer similar structural and corrosion performance but with heat resistance up to 600 °C (1,112 °F).
The RMIT team believes that given its lightweight design, high strength, and heat resistance, its metamaterial would be an excellent choice for drones employed in monitoring and combating wildfires across Australia and the United States. At present, drones have been produced using solid titanium, which possesses the strength and heat resistance necessary to endure wildfires but is excessively heavy for long-distance flights on a single battery charge. Using parts made from the printed titanium metamaterial would enable drones to fly further and longer before requiring a recharge, affording firefighters a better opportunity to assess a wildfire’s extent and progression.
Other possible applications mentioned in the research paper, “Titanium Multi-Topology Metamaterials with Exceptional Strength,” published in Advanced Materials, include biomedical implants and aerospace components.
More about advanced manufacturing: 3D-Printed Bicycle Headed for Olympics
One present difficulty with using laser powder bed fusion of titanium is that the manufacturing time is quite slow. “A one-kilogram titanium metamaterial part might take about 10 hours for one single laser beam to print,” Qian said.
Adding more lasers could significantly reduce print time. Engineers also aim to enhance the printing speed of each laser beam by up to one hundred times the current printing speeds. As the printing time decreases and competition within the 3D printing industry increases, the time and cost to manufacture complex, porous metal parts will improve.
Nicole Imeson is a technology writer in Calgary, Alta.
Inspired by nature’s sophisticated designs, researchers at the Royal Melbourne Institute of Technology (RMIT) in Australia have combined two types of lattice structures to create a metamaterial they printed in titanium. The metamaterial boasts high strength, lightweight properties, corrosion resistance, and high-temperature durability. The researchers also found that it was capable of uniformly distributing stress, reducing deformation, and enhancing strength.
Engineers have for decades attempted to produce materials that mimic the combination of strength and airiness found in natural materials. Two types of repeating lattice structures that have been tested are hollow strut lattices (HSL) and thin plate lattices (TPL). But neither proved to have been successful. HSLs utilize interconnected channels to distribute forces throughout the structure while maintaining a lightweight design. Despite this, they fail to evenly distribute forces, resulting in failure points where the channels intersect. Conversely, TPLs employ interconnected thin plates in a lattice configuration to evenly distribute stress, albeit with solid plates.
A metamaterial is a type of composite where the properties arise from its engineered structure, rather than the bulk materials it is made of. The material engineered by the RMIT researchers combines the HSLs and TPLs into a metamaterial that negates the weaknesses of each type of lattice. The metamaterial is capable of uniformly distributing stress, reducing deformation, and providing unparalleled strength.
According to Ma Qian, a distinguished professor of advanced manufacturing and materials at RMIT, “The more uniform the distribution of the stress throughout the structure, the better the performance of the structure. Our design has a reasonably uniform distribution of stress; therefore, the performance improves a lot.”
Such a complicated structure could not be manufactured using conventional manufacturing methods. Instead, the researchers relied on laser powder bed fusion, an additive manufacturing process that prints 3D parts in layers using metal powder and a laser beam, essentially drawing the part in a series of stacked 2D layers. This process not only enabled intricate and non-uniform designs but also permitted the removal of excess, unfused powder from the part after printing, creating a porous network within the part.
“3D metal printing has offered unprecedented design and manufacturing abilities for us to create new metallic materials for various purposes,” Qian said.
Researchers crafted the metamaterial using titanium alloy Ti-6Al-4V, known for its corrosion resistance, especially in marine or seawater environments, high strength, and heat resistance up to 350 °C (662 °F). This alloy is often used in critical applications, notably aerospace and biomechanics for implants and prostheses. Additionally, the RMIT team proposed that if the metamaterial is printed from another titanium alloy, Ti-SF61, it would offer similar structural and corrosion performance but with heat resistance up to 600 °C (1,112 °F).
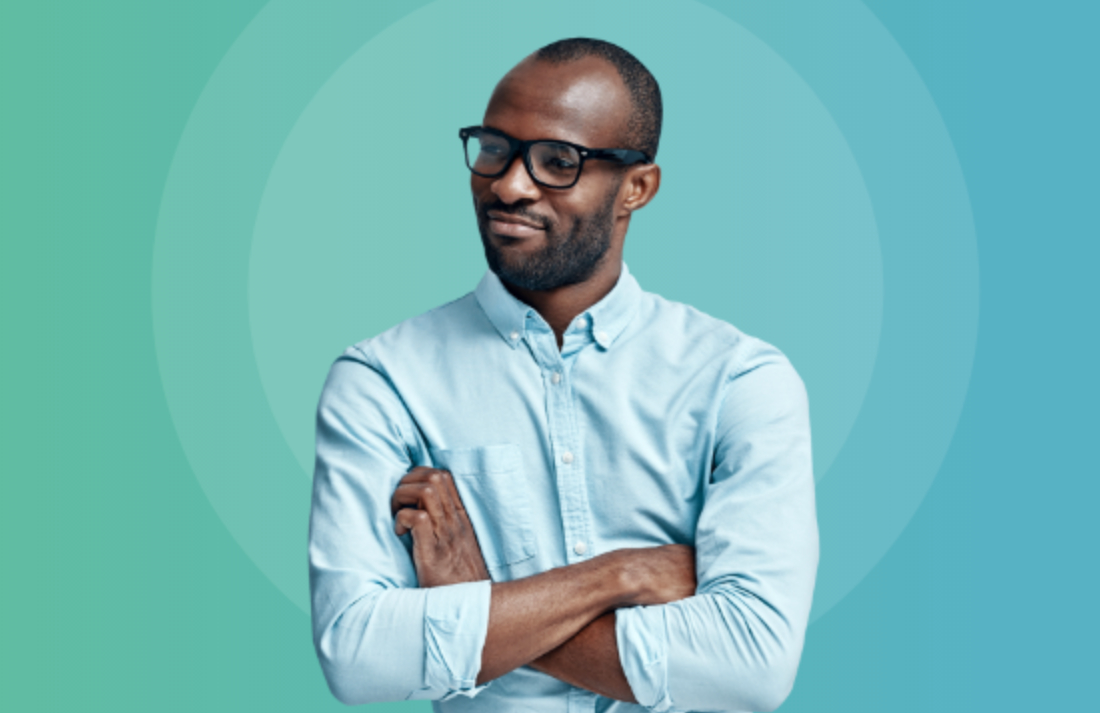
Discover the Benefits
Whether you’re an experienced professional or just starting your career, ASME’s membership community, resources and tools can help you with your lifelong journey.
Other possible applications mentioned in the research paper, “Titanium Multi-Topology Metamaterials with Exceptional Strength,” published in Advanced Materials, include biomedical implants and aerospace components.
More about advanced manufacturing: 3D-Printed Bicycle Headed for Olympics
One present difficulty with using laser powder bed fusion of titanium is that the manufacturing time is quite slow. “A one-kilogram titanium metamaterial part might take about 10 hours for one single laser beam to print,” Qian said.
Adding more lasers could significantly reduce print time. Engineers also aim to enhance the printing speed of each laser beam by up to one hundred times the current printing speeds. As the printing time decreases and competition within the 3D printing industry increases, the time and cost to manufacture complex, porous metal parts will improve.
Nicole Imeson is a technology writer in Calgary, Alta.
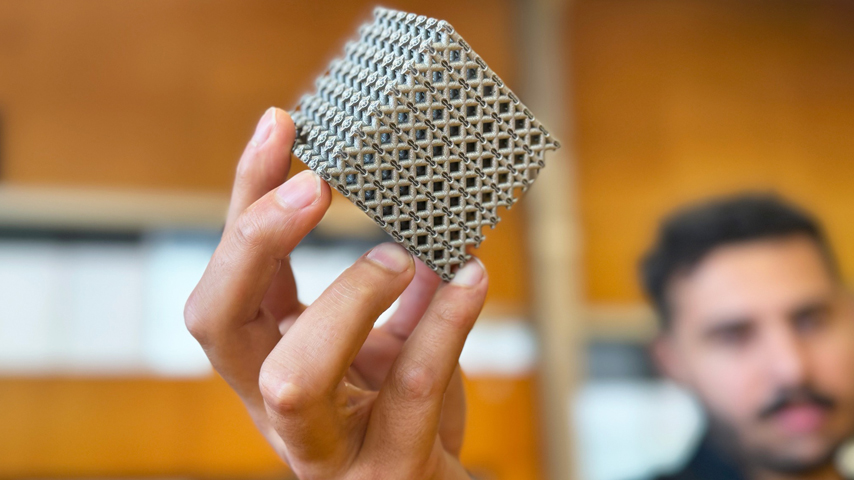
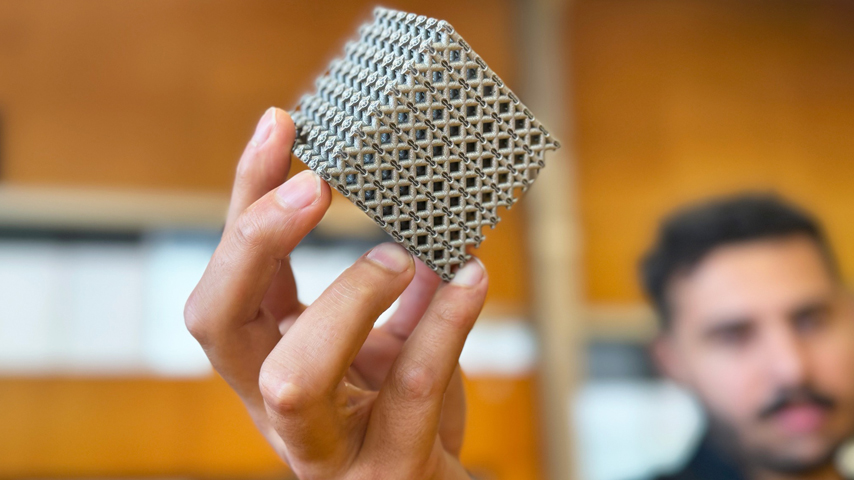