New Metal Alloy Is Stronger than the Toughest Aerospace Materials
New Metal Alloy Is Stronger than the Toughest Aerospace Materials
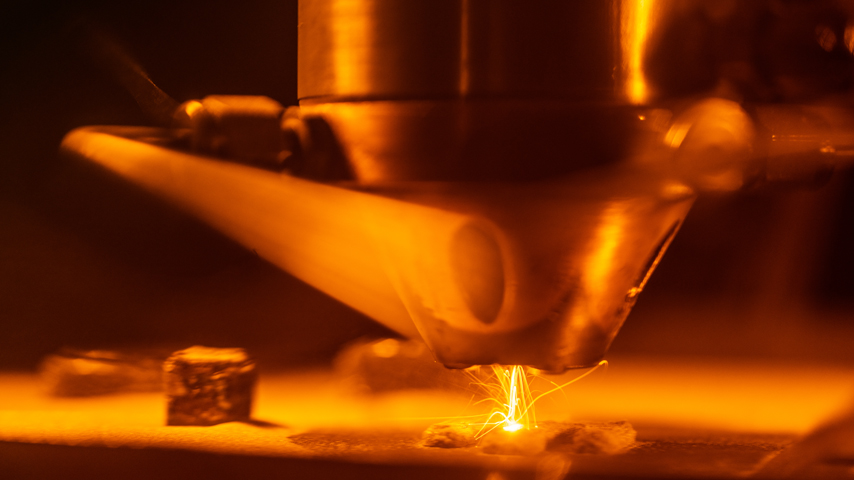
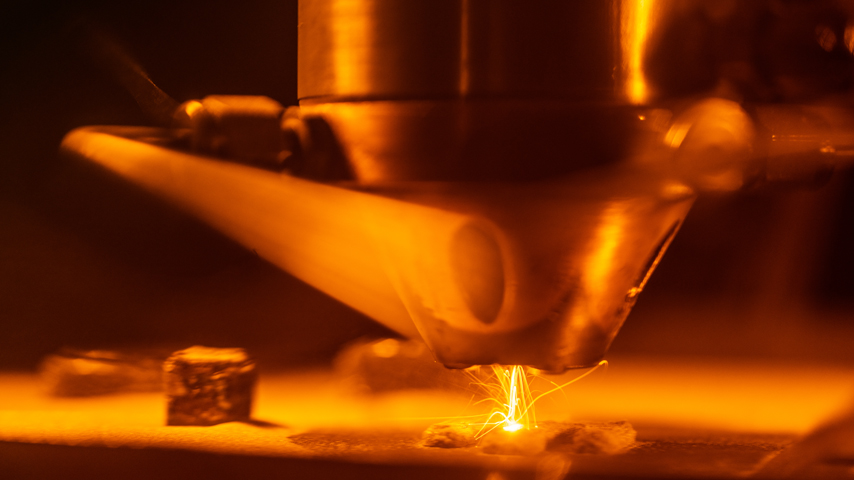
Scientists at Sandia National Laboratories have created a high-performance metal super-alloy that is stronger than the toughest materials currently used in high-temperature industrial applications.
A team of researchers from Sandia National Laboratory, Ames National Laboratory, Iowa State University, and Bruker Corporation used a unique additive manufacturing method to create a high-performance metal alloy that is stronger and lighter than the toughest materials currently used in high-temperature applications, such as gas turbine machinery. Because of its remarkably high heat resistance, the superalloy could allow turbines to operate at higher temperatures, thereby generating more electricity and producing less carbon.
Experiments showed that the new superalloy—42 percent aluminum, 25 percent titanium, 13 percent niobium, 8 percent zirconium, 8 percent molybdenum, and 4 percent tantalum—was stronger at 800 °C (1,472 °F) than many other high-performance alloys.
Become a Member: How to Join ASME
“We’re showing that this material can access previously unobtainable combinations of high strength, low weight, and high-temperature resiliency,” said Andrew Kustas, a principal member of the technical staff in the Material, Physical, and Chemical Sciences Center at Sandia National Laboratories. “We think part of the reason we achieved this is because of the additive manufacturing approach.”
A highlight of this research is that it shows how additive manufacturing (AM) can be used to easily produce functional samples of new alloy materials. The team used a 3D printer to melt together exact amounts of powdered metals and then immediately print a sample of it for testing.
“We used a method called laser engineered net shaping [LENS], which is a type of directed energy deposition 3D printing,” said Kustas.
LENS was first developed, patented, and commercialized by Sandia National Laboratories in the mid-1990s. It uses fluidized powders as starting material feedstock that are blown toward a melt pool, which is created by a high-power laser. As powder is blown into the melt pool, it rapidly solidifies into a solid metal layer or weld bead. Parts are then constructed with this method in a layerwise manner, following a computer-generated 3D solid model.
“A primary and unique advantage of this approach compared to other manufacturing methods, including other 3D printing techniques, is the ability to use small powder batches as feedstock, on the order of only a few hundred grams, which is ideal for exploring expensive and experimental metals/alloys,” said Kustas. “Multiple reservoirs are used to contain the powder feedstock, from which powder is transferred to the weld pool. Independent control of the powder flow rates from each reservoir enables rapid development of custom and gradient alloys in a single part.”
More for You: 9 Material Discoveries that Could Transform Manufacturing
In general, the biggest surprise for the team was how strong the material was during hardness testing.
“The alloy had a room temperature hardness of 10-15 GPa, and an average 8 GPa hardness at a temperature of 800 Celsius,” said Kustas. “Overall, the maximum hardness or strength of this alloy is more than 300 percent greater than Inconel 718, which is a conventional nickel-based superalloy currently used in aviation and aerospace applications. We used a range of mechanical tests to determine these properties, including variable-temperature nanoindentation, micro-scratch and Vickers microindentation methods.”
Also, in general, the alloy may permit operation of these systems at a reduced overall weight and higher temperatures than are currently allowable with state-of-the-art superalloys, allowing for higher energy efficiency during operation. “For instance, this alloy, or a family of alloys from this material system, might be recommended in various standards in the future, such as the ASME Boiler and Pressure Vessel codes for high performance alloys,” said Kustas.
Perhaps the biggest concern about this discovery is scalability. While the alloy shows promise in terms of retaining high strength at high temperatures, there are some challenges that need to be overcome. For example, the alloy was prone to cracking during the manufacturing of small-scale laboratory samples, which could be a considerable concern for end-use applications that require large geometries.
“Furthermore, additional material properties characterization will be critical, such as the alloy creep behavior and oxidation behavior,” said Kustas. “Our team is excited to continue exploring the alloy system to find other candidate alloys that may offer other unique combinations of properties.”
Mark Crawford is a technology writer in Corrales, N.M.
Experiments showed that the new superalloy—42 percent aluminum, 25 percent titanium, 13 percent niobium, 8 percent zirconium, 8 percent molybdenum, and 4 percent tantalum—was stronger at 800 °C (1,472 °F) than many other high-performance alloys.
Become a Member: How to Join ASME
“We’re showing that this material can access previously unobtainable combinations of high strength, low weight, and high-temperature resiliency,” said Andrew Kustas, a principal member of the technical staff in the Material, Physical, and Chemical Sciences Center at Sandia National Laboratories. “We think part of the reason we achieved this is because of the additive manufacturing approach.”
A new role for AM
A highlight of this research is that it shows how additive manufacturing (AM) can be used to easily produce functional samples of new alloy materials. The team used a 3D printer to melt together exact amounts of powdered metals and then immediately print a sample of it for testing.
“We used a method called laser engineered net shaping [LENS], which is a type of directed energy deposition 3D printing,” said Kustas.
LENS was first developed, patented, and commercialized by Sandia National Laboratories in the mid-1990s. It uses fluidized powders as starting material feedstock that are blown toward a melt pool, which is created by a high-power laser. As powder is blown into the melt pool, it rapidly solidifies into a solid metal layer or weld bead. Parts are then constructed with this method in a layerwise manner, following a computer-generated 3D solid model.
“A primary and unique advantage of this approach compared to other manufacturing methods, including other 3D printing techniques, is the ability to use small powder batches as feedstock, on the order of only a few hundred grams, which is ideal for exploring expensive and experimental metals/alloys,” said Kustas. “Multiple reservoirs are used to contain the powder feedstock, from which powder is transferred to the weld pool. Independent control of the powder flow rates from each reservoir enables rapid development of custom and gradient alloys in a single part.”
More for You: 9 Material Discoveries that Could Transform Manufacturing
In general, the biggest surprise for the team was how strong the material was during hardness testing.
“The alloy had a room temperature hardness of 10-15 GPa, and an average 8 GPa hardness at a temperature of 800 Celsius,” said Kustas. “Overall, the maximum hardness or strength of this alloy is more than 300 percent greater than Inconel 718, which is a conventional nickel-based superalloy currently used in aviation and aerospace applications. We used a range of mechanical tests to determine these properties, including variable-temperature nanoindentation, micro-scratch and Vickers microindentation methods.”
Moving forward
The team is interested in exploring whether advanced computer modeling techniques can help researchers discover more members of what could be a new class of high-performance, additive-manufactured superalloys.
Also, in general, the alloy may permit operation of these systems at a reduced overall weight and higher temperatures than are currently allowable with state-of-the-art superalloys, allowing for higher energy efficiency during operation. “For instance, this alloy, or a family of alloys from this material system, might be recommended in various standards in the future, such as the ASME Boiler and Pressure Vessel codes for high performance alloys,” said Kustas.
Perhaps the biggest concern about this discovery is scalability. While the alloy shows promise in terms of retaining high strength at high temperatures, there are some challenges that need to be overcome. For example, the alloy was prone to cracking during the manufacturing of small-scale laboratory samples, which could be a considerable concern for end-use applications that require large geometries.
“Furthermore, additional material properties characterization will be critical, such as the alloy creep behavior and oxidation behavior,” said Kustas. “Our team is excited to continue exploring the alloy system to find other candidate alloys that may offer other unique combinations of properties.”
Mark Crawford is a technology writer in Corrales, N.M.