Metal 3D Printing for Orthopedics
Metal 3D Printing for Orthopedics
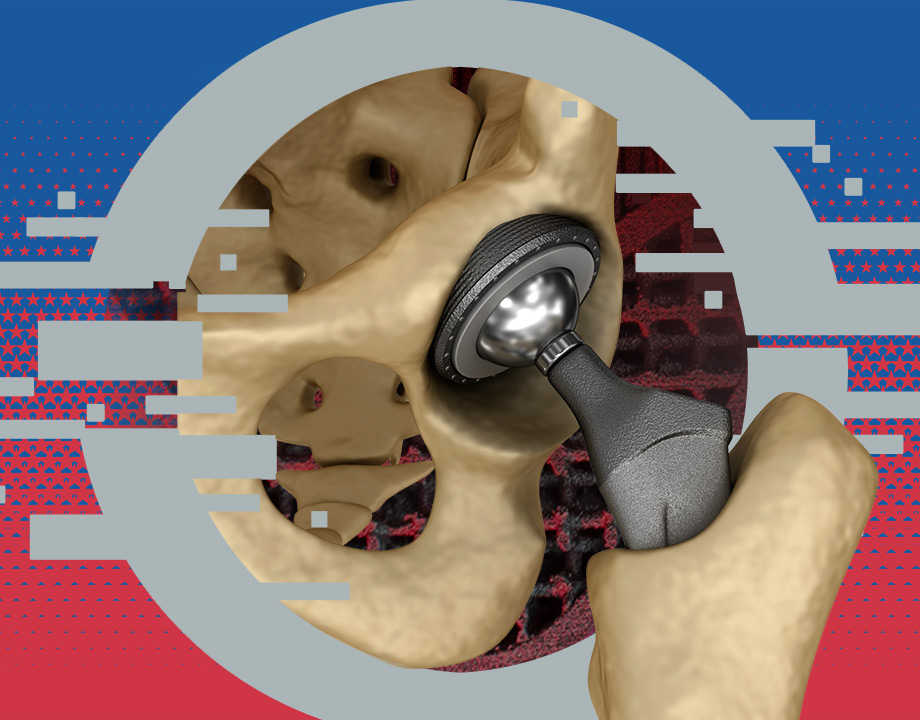
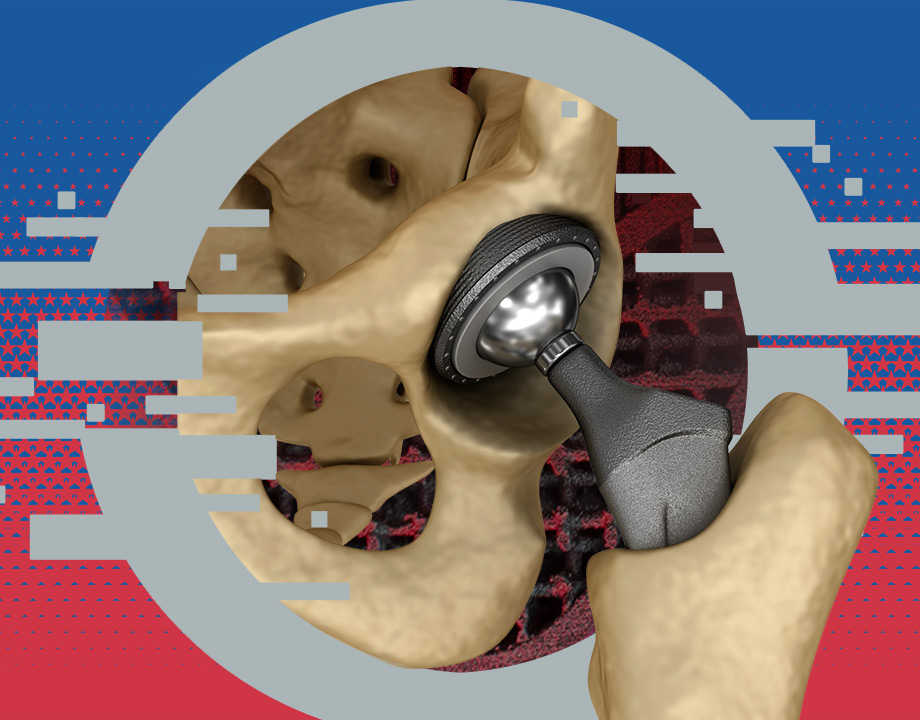
Advances in 3D printing technology, software, and materials are making it possible to mass-produce orthopedic devices, implants, and instruments from metals.
While initially AM focused on plastics and polymers, now it can produce reliable, high-performance, and FDA-compliant metal components from metal powders. This is of keen interest to orthopedic device manufacturers, who have long favored metals for their products, but could only produce them using subtractive machining methods, which are expensive and time-consuming.
Orthopedic device manufacturers prefer to use such metals as titanium, cobalt-chrome, and stainless steel. Although metal 3D printing has made great advances in the last few years, it is still mostly used for prototypes or patient-specific implants, where speed and volume production are not top priorities.
Being able to mass-produce orthopedic implants and instruments depends on finding the best combination of product design, AM process, and materials that maximizes speed, reduces steps, and minimizes or eliminates post-printing processing. Here are some technological advancements that are changing the industry.
New 3D Printing Methods
An expanding number of 3D printing methods can print metals, but all have limitations.
Powder bed fusion (variations include selective laser sintering and selective laser melting) fuses metal powders into layers with lasers or electron beams and is used to make metallic implants. However, it tends to be slow and quality can vary—drawbacks to mass production.
Further Reading: 3D Printing Overcoming Biocompatibility Challenge
Directed energy deposition (DED) uses a nozzle to deposit metal feedstock while a laser or electron beam melts it. “DED delivers rapid production time and fully dense parts, making it the fastest additive manufacturing technology to date,” said Matt Sand, president of 3DEO, an AM company. However, the rough surface finish requires post-processing, which adds time and cost.
Binder jetting is yet another fast powder-bed process that uses an inkjet to deposit a liquid binder onto a powder layer in the shape of the part. The resulting part is then sintered to achieve final density. “While binder jetting is low-cost and fast, parts require infiltration to prevent shrinkage and post-processing to improve surface finish,” Sand said.
Mass Production
Rapid advances in 3D printing technology—especially in quality, materials, and speed—have made it possible to mass-produce orthopedic implants and instruments. Whether or not high-volume production can be carried out with 3D printing depends on how the process can be optimized to maximize speed and reduce cost.
Much of the increase in 3D printing capabilities (especially speed) is the result of software advances. These include methods for converting patient image data into 3D models.
For example, Betatype, a London-based additive manufacturing software company, can double the production rate of 3D-printed orthopedic implants by using software that optimizes workflow. This includes using faster file formats for transmitting imaging data and taking advantage of the 3D printer’s build volume by stacking models on top of each other. A study showed that this method can produce 800 lumbar cages at one time.
Renishaw, a U.K.-based company that specializes in manufacturing technology, recently developed a metal 3D printer suitable for higher production levels. “This meant getting the build rates as high as possible while bringing the cost per part down,” said Stephen Anderson, additive manufacturing business manager for Renishaw is the U.S.
“We decided to put four 500-watt lasers into an existing 250 x 250 x 350-mm machine to deliver maximum throughput and part quality for smaller workpieces.” This did, however, require some significant engineering work, including a chiller to cool the optical system and a patented vacuum preparation system.
Related Bioengineering Blog Post: Advanced Design and Manufacturing Tools Empower Personalized Medicine
“Having four lasers provides great flexibility,” Anderson said. “If you’re building a large workpiece, then you can bring all four lasers to bear on that one part. Specific lasers might be responsible for the bulky internal geometry, for instance, while others trace the outside of the part. Alternatively, if the build chamber is filled with a number of small components, you can assign an individual laser to each, thereby maximizing production.”
What’s Next
3D printing technology brings many advantages to the manufacturing of metallic orthopedic devices, “including the capability of personalized designs, the fabrication of structures with complex geometries, and the reduction of manufacturing time and medical costs,” said J. Ni, professor of bioengineering at the University of California, Los Angeles. “However, this method is still in its infant stages for biomedical applications, and there are many challenges before its clinical use is widespread.”
One of the greatest challenges is repeatability of quality.
“As metal 3D printing becomes more mainstream, process validation and monitoring become increasingly critical,” Anderson said. “It’s only through robust process monitoring and strict adherence to standards that manufacturers will be able to assure their customers that the 500th part in a production run is identical to the first one, and that the parts you build next year will be identical to those built today, regardless of the printer used or the facility it came from.
“Achieving this will require a ‘digital fingerprint’ that carries with it a record of the build process and documents the build parameters, the equipment status, the raw materials, gases, and a host of other variables that can affect the build process.”
Mark Crawford is a technology writer based in Corrales, N.M.
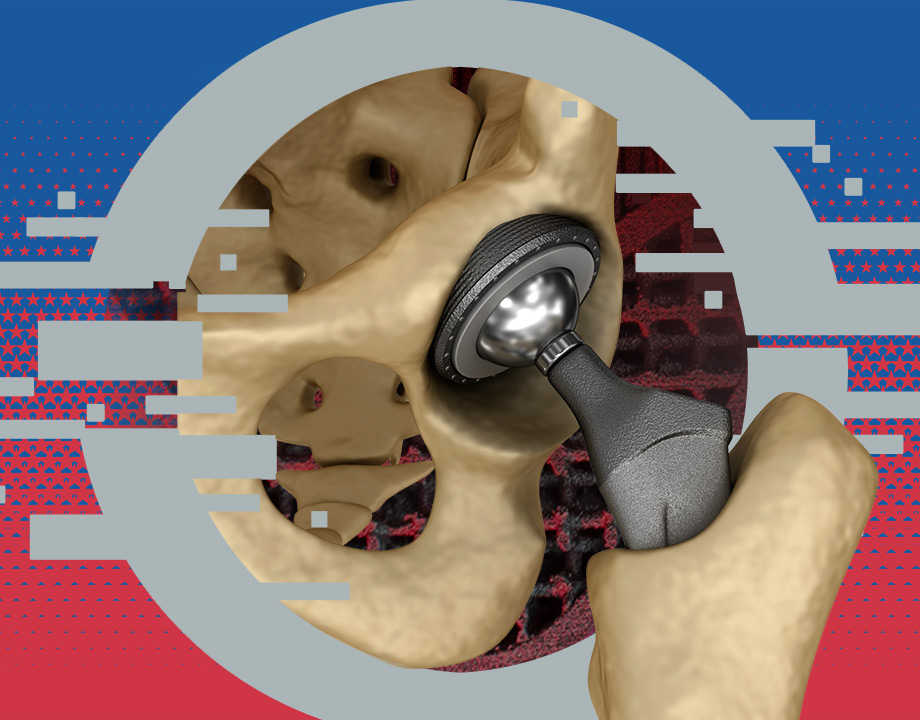
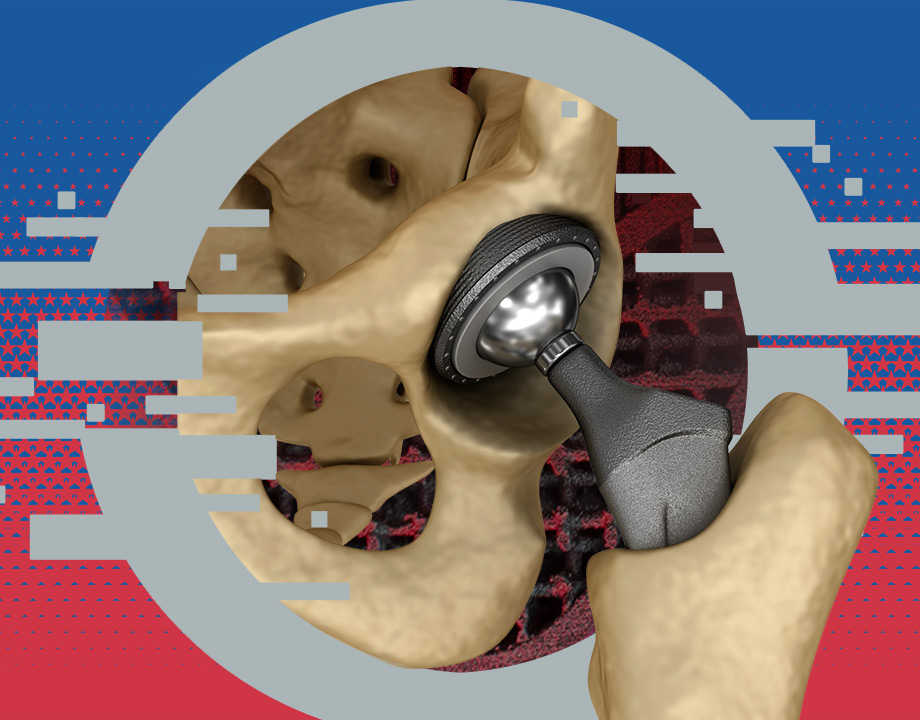