Manufacturing Blog: Engineering a Future of Sustainable Manufacturing
Manufacturing Blog: Engineering a Future of Sustainable Manufacturing
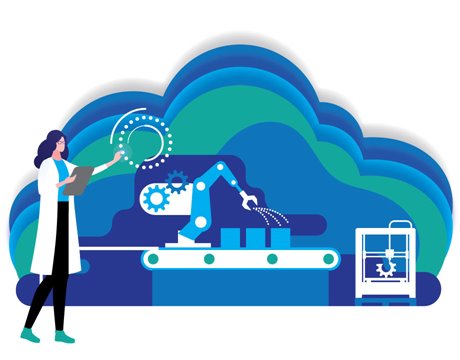
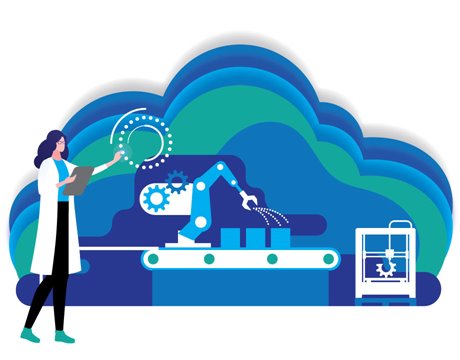
Sustainable manufacturing will change how engineers think and work by creating a process that is lean, efficient, and environmentally conscientious.
Does an engineer have to sacrifice production output to be environmentally sustainable? According to Dassault Systemes, the answer is no.
Sustainable manufacturing and efficient engineering go hand in hand. The outcome is an improved manufacturing process that is not only lean but also productive.
Last month I attended the Manufacturing in the Age of Experience event hosted by Dassault Systemes in Shanghai, China. The key message conveyed was that in today's world—with the impending climate crisis and resource scarcity—engineers need to manufacture products more sustainably; the production process cannot be a burden on the world.
But what exactly is sustainable manufacturing, and what is the engineer’s role in the process?
Defining sustainable manufacturing is the first step.
Sustainable manufacturing rests on three main pillars, as listed by Dassault Systemes.
"For the longest time, people viewed sustainability as helping improve the planet. And while we all agree with that, that's just one element of sustainability," said Eric Green, vice president and managing director of user experience at Dassault Systemes.
"In addition to that, an industrial environment that focuses on lean manufacturing helps reinforce the idea of sustainability, and helps drive operational efficiencies. And to do that, we have to orchestrate across the different stakeholders."
You May Also Like: Six Lean Principles for an Industry 4.0 World
The deconstruction of silos is vital for sustainable manufacturing. Often, when problems occur on the manufacturing floor, manufacturing engineers have to solve them to ensure production doesn’t stop. However, if the problem is not recorded, the design engineers are unaware of the underlying issue. The production process has an internal process of waste and has lost efficiency.
The opposite is also true. Design changes occur and do not appropriately flow down to the manufacturing team, creating incorrect parts and waste.
The goal of sustainable manufacturing is to reduce these wasteful steps and to create a continuous feedback loop of efficiency—this is where the digitization of the engineering process comes in to play.
Revisiting the three pillars of sustainable manufacturing, the digital tools we have today are crucial to solving the problems.
Digital tools bring computer-aided modeling influenced by machine learning, simulation of both products and the manufacturing line, and digital twins from the beginning of the production process till the product delivery. These will be essential engineering tools to help reduce mistakes before they occur in the real world.
Simulation optimization, such as the digital tools on the Dassault Systemes 3DExperience platform, will inform engineers of a better solution by helping reduce the amount of material needed to produce a part. It can also help to assemble a production line in the most cost-efficient way possible. Digital tools can guide engineers to not overstock on materials and hardware, resulting in less waste.
"Simulation optimization can run manufacturing more efficiently to help provide the products at the right time based on demand, and in doing so, consume less inventory and maximize the time and the amount of labor spent," Green said.
Recommended for You: The State of American Manufacturing 2019
This results not just in production efficiency but also in the carbon footprint reduction. Engineers can help to consume less energy and raw materials during the manufacturing process.
Of course, the key to all of this is not only to create a future workforce but to evolve the current workforce; to use the new toolset at their disposal to create more sustainable solutions.
Part of this will be to retrain and educate incoming and current engineers on new digital platforms and connected networks. Engineers resistant to change need to be shown proof that there is a benefit to adopting new tools.
"So a lot of times, the older workforce, they do things, and they make decisions based upon the way they've done business for years, and that's how they were taught. But they don't necessarily have the information or the understanding of the repercussions of their decision because they lack the data and the tools to understand those implications," Green said. "By providing them the data to see their historical decisions, which created additional problems in the manufacturing process, they can make new informed decisions, and come to their own conclusions on how to improve the process."
Editor's Pick: Who Are the Engineers of the Future?
Making sustainability core to the job will be essential. Engineers don't want another checklist at the end of the day. Providing them with a digital toolset that can help analyze their decisions before they are made can become a new set of checks and balances in the manufacturing process.
"The third pillar of sustainable manufacturing, is the notion of empowering the workforce, to make decisions," Green said. "We look forward to the future and enabling them to not only make decisions but to be creative and innovative and how they go about work and finding ways to do things differently."
Carlos M. Gonzalez is special projects manager.
Sustainable manufacturing and efficient engineering go hand in hand. The outcome is an improved manufacturing process that is not only lean but also productive.
Last month I attended the Manufacturing in the Age of Experience event hosted by Dassault Systemes in Shanghai, China. The key message conveyed was that in today's world—with the impending climate crisis and resource scarcity—engineers need to manufacture products more sustainably; the production process cannot be a burden on the world.
But what exactly is sustainable manufacturing, and what is the engineer’s role in the process?
Defining sustainable manufacturing is the first step.
What is Sustainable Manufacturing?
Sustainable manufacturing rests on three main pillars, as listed by Dassault Systemes.
- Optimized lean engineering operations: Creating a manufacturing process that eliminates waste, reduces overproduction, errors, scrap, and delay.
- Unified Work Process: Establishing a collaborative workflow across all engineering departments that promote transparency and efficiency.
- Workforce of Tomorrow: Educating a future workforce that uses the latest tools available to be more efficient, collaborative, and safe.
"For the longest time, people viewed sustainability as helping improve the planet. And while we all agree with that, that's just one element of sustainability," said Eric Green, vice president and managing director of user experience at Dassault Systemes.
"In addition to that, an industrial environment that focuses on lean manufacturing helps reinforce the idea of sustainability, and helps drive operational efficiencies. And to do that, we have to orchestrate across the different stakeholders."
You May Also Like: Six Lean Principles for an Industry 4.0 World
The deconstruction of silos is vital for sustainable manufacturing. Often, when problems occur on the manufacturing floor, manufacturing engineers have to solve them to ensure production doesn’t stop. However, if the problem is not recorded, the design engineers are unaware of the underlying issue. The production process has an internal process of waste and has lost efficiency.
The opposite is also true. Design changes occur and do not appropriately flow down to the manufacturing team, creating incorrect parts and waste.
The goal of sustainable manufacturing is to reduce these wasteful steps and to create a continuous feedback loop of efficiency—this is where the digitization of the engineering process comes in to play.
How Do We Become Efficient?
Revisiting the three pillars of sustainable manufacturing, the digital tools we have today are crucial to solving the problems.
Digital tools bring computer-aided modeling influenced by machine learning, simulation of both products and the manufacturing line, and digital twins from the beginning of the production process till the product delivery. These will be essential engineering tools to help reduce mistakes before they occur in the real world.
Simulation optimization, such as the digital tools on the Dassault Systemes 3DExperience platform, will inform engineers of a better solution by helping reduce the amount of material needed to produce a part. It can also help to assemble a production line in the most cost-efficient way possible. Digital tools can guide engineers to not overstock on materials and hardware, resulting in less waste.
"Simulation optimization can run manufacturing more efficiently to help provide the products at the right time based on demand, and in doing so, consume less inventory and maximize the time and the amount of labor spent," Green said.
Recommended for You: The State of American Manufacturing 2019
This results not just in production efficiency but also in the carbon footprint reduction. Engineers can help to consume less energy and raw materials during the manufacturing process.
The Evolution of the Workforce
Of course, the key to all of this is not only to create a future workforce but to evolve the current workforce; to use the new toolset at their disposal to create more sustainable solutions.
Part of this will be to retrain and educate incoming and current engineers on new digital platforms and connected networks. Engineers resistant to change need to be shown proof that there is a benefit to adopting new tools.
"So a lot of times, the older workforce, they do things, and they make decisions based upon the way they've done business for years, and that's how they were taught. But they don't necessarily have the information or the understanding of the repercussions of their decision because they lack the data and the tools to understand those implications," Green said. "By providing them the data to see their historical decisions, which created additional problems in the manufacturing process, they can make new informed decisions, and come to their own conclusions on how to improve the process."
Editor's Pick: Who Are the Engineers of the Future?
Making sustainability core to the job will be essential. Engineers don't want another checklist at the end of the day. Providing them with a digital toolset that can help analyze their decisions before they are made can become a new set of checks and balances in the manufacturing process.
"The third pillar of sustainable manufacturing, is the notion of empowering the workforce, to make decisions," Green said. "We look forward to the future and enabling them to not only make decisions but to be creative and innovative and how they go about work and finding ways to do things differently."
Carlos M. Gonzalez is special projects manager.