Lobster Shell Patterns May Strengthen 3D-Printed Concrete
Lobster Shell Patterns May Strengthen 3D-Printed Concrete
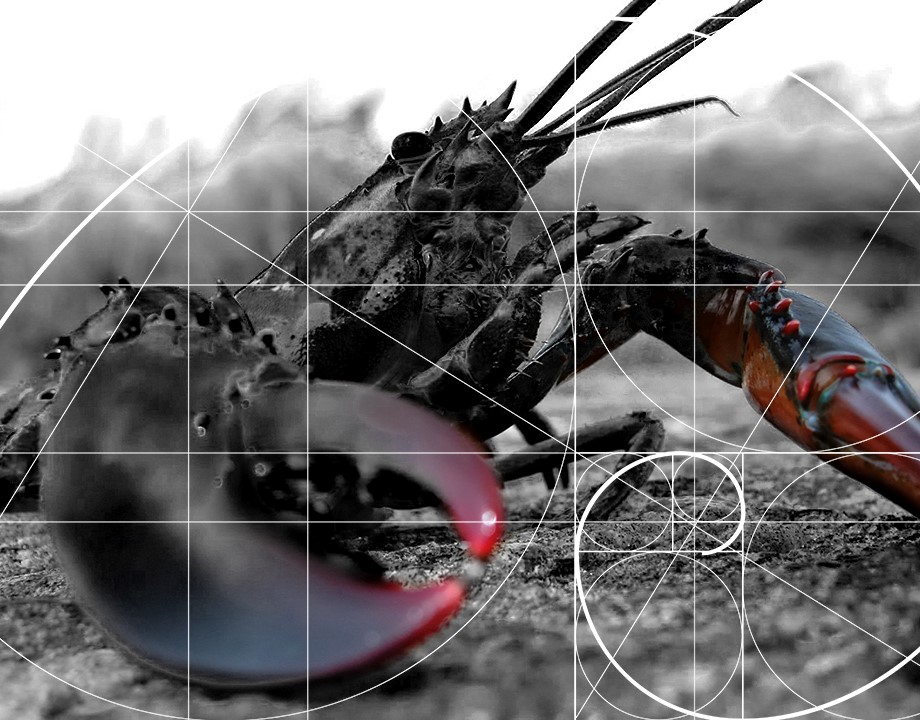
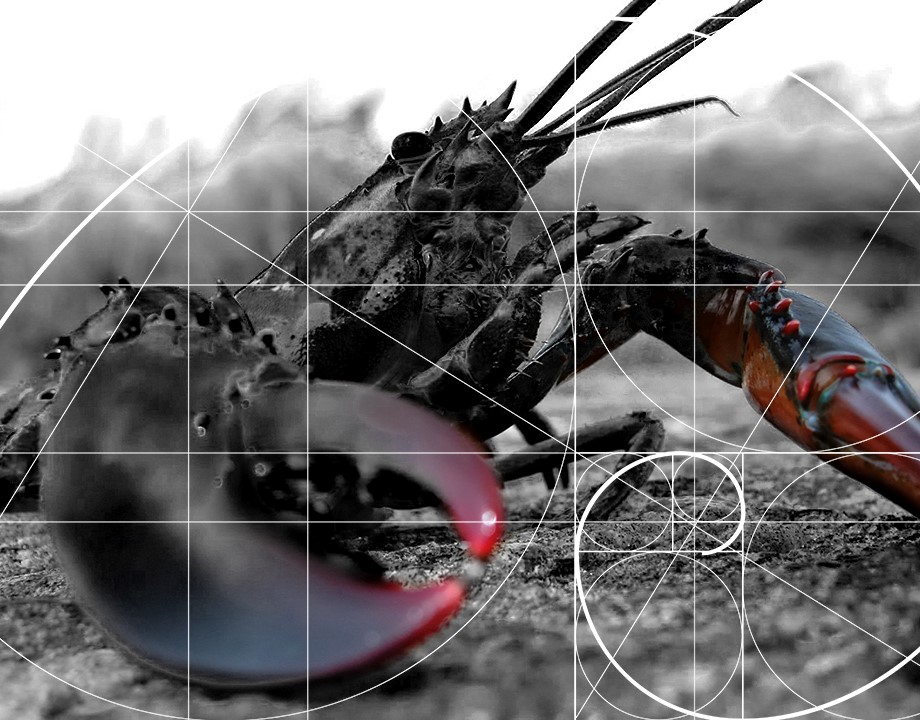
3D printing may strengthen concrete by laying patterns that harden like a lobster’s shell.
Bioinspired designs can be beneficial in the design and construction of strong, resilient structures, particularly of those creatures that for millennia come clad in their own strong, resilient structures. The lobster, specifically, lives in one of the toughest shells on the planet, protecting it from the pressures of more than a quarter of a mile of sea water and the fiercest predators.
What makes the lobster so strong? How can we model our buildings on it? These were the questions that came to Jonathan Tran when he was a graduate student in the U.S. more than a decade ago. Now a senior lecturer in the civil and infrastructure engineering department of Melbourne’s RMIT University, he is a co-author of a recently published paper investigating 3D printing of concrete using structural patterns similar to those found in a lobster’s shell.
“Seafood is one of my favorites, and lobster in the U.S. is some of the best in the world,” he said. “You get a lobster shell on your finger and you start to wonder, why is it so stiff? Can we mimic it?”
When he first had those questions, 3D printers were scarce and no one was thinking of using additive technologies to build walls.
Now he has some answers to those questions, and a method for printing concrete that may make the material stronger. It comes straight from the lobster shell, which, despite appearances is not one thin layer of material.
Editor's Pick: Is 3D Printing the Future of Manufacturing?
“If you look at it very closely in a microscope,” said Tran, “it’s not a simple single layer, but composed of hundreds of thinner layers.”
Those layers twist in an organized architecture. But this structuring is not all that gives the lobster’s exoskeleton its strength. It’s also chitin, the material of which the shell is made. Tiny stretchable nanofibers of the substance are stacked upon each other hierarchically, making the lobster’s armor light in weight but strong and tough.
To make his 3D printing as crustaceanly strong as the lobster’s shell, Tran borrowed both from both the architecture and the makeup of the bottom dweller’s exterior. “Normally you use a mold, cement, sand, and water and steel reinforcement oriented in one direction and that’s it,” he said. “But with 3D printing we can design the pattern of the filament as it’s printed out.”
Reader's Choice: Video: Leveraging Data for Additive Manufacturing
The printer roughly duplicates those patterns, making parallel lines in one direction for one layer and changing the angle by 30, 45, or 90 degrees for the next. “Specifically, unidirectional (0°), cross-ply (0°/90°), quasi-isotropic (0°/ ± 45°/90°), and helicoidal patterns (with pitch angles of 10°, 20°, and 30°) are used to create unidirectional, bidirectional, and multidirectional layers in printed objects without and with 0.75% by volume of 6 mm-long steel fibers,” wrote Tran and his co-authors in the paper, “Influences of Printing Pattern on Mechanical Performance of Three-Dimensional-Printed Fiber-Reinforced Concrete.”
The filaments that Tran is using are as thin as human hairs, and make up two percent of the concrete. As the printer prints, these delicate fibers are stretched out in the direction the printer is moving. X-ray tomography has revealed the fibers stay oriented in different directions for different layers after the concrete hardens.
The result is a bioinspired concrete that’s 1.5 times stronger than a standard mix. But it’s not just superior in terms of brute strength. It also breaks better. When conventional concrete cracks, the fissures spread out in a plane, allowing them to extend deep into a structure.
“The fracture surface of bio-inspired concrete is twisted in a different direction,” said Tran. “It doesn’t go straight from top to bottom. Because a crack has to travel a longer path to complete the failure, more energy is needed to break bioinspired concrete.”
More for You: Diligence is Required When on the Hunt for Good AM Solutions
The results show promise for building components or infrastructure. But more work still must be done before it is put to use. The bioinspired concrete is fairly weak when still wet, so its use in structures is limited for now. Curved dome-like structures are similarly susceptible to gravity.
Rebar, of course, is used to strengthen concrete components and structures, but its use with this concrete still must be investigated. For the construction field, there are still limited studies investigating the changes of different internal architectures of cement-based materials on mechanical behavior, the authors noted.
Tran is thinking big, and looking to the heavens. He hopes his work will help change construction on this planet, but off the planet as well. “If you’re printing on the Moon or Mars, it needs to be fully autonomous,” he said.
Michael Abrams is a technology writer based in Westfield, N.J.
What makes the lobster so strong? How can we model our buildings on it? These were the questions that came to Jonathan Tran when he was a graduate student in the U.S. more than a decade ago. Now a senior lecturer in the civil and infrastructure engineering department of Melbourne’s RMIT University, he is a co-author of a recently published paper investigating 3D printing of concrete using structural patterns similar to those found in a lobster’s shell.
“Seafood is one of my favorites, and lobster in the U.S. is some of the best in the world,” he said. “You get a lobster shell on your finger and you start to wonder, why is it so stiff? Can we mimic it?”
When he first had those questions, 3D printers were scarce and no one was thinking of using additive technologies to build walls.
Now he has some answers to those questions, and a method for printing concrete that may make the material stronger. It comes straight from the lobster shell, which, despite appearances is not one thin layer of material.
Editor's Pick: Is 3D Printing the Future of Manufacturing?
“If you look at it very closely in a microscope,” said Tran, “it’s not a simple single layer, but composed of hundreds of thinner layers.”
Those layers twist in an organized architecture. But this structuring is not all that gives the lobster’s exoskeleton its strength. It’s also chitin, the material of which the shell is made. Tiny stretchable nanofibers of the substance are stacked upon each other hierarchically, making the lobster’s armor light in weight but strong and tough.
To make his 3D printing as crustaceanly strong as the lobster’s shell, Tran borrowed both from both the architecture and the makeup of the bottom dweller’s exterior. “Normally you use a mold, cement, sand, and water and steel reinforcement oriented in one direction and that’s it,” he said. “But with 3D printing we can design the pattern of the filament as it’s printed out.”
Reader's Choice: Video: Leveraging Data for Additive Manufacturing
The printer roughly duplicates those patterns, making parallel lines in one direction for one layer and changing the angle by 30, 45, or 90 degrees for the next. “Specifically, unidirectional (0°), cross-ply (0°/90°), quasi-isotropic (0°/ ± 45°/90°), and helicoidal patterns (with pitch angles of 10°, 20°, and 30°) are used to create unidirectional, bidirectional, and multidirectional layers in printed objects without and with 0.75% by volume of 6 mm-long steel fibers,” wrote Tran and his co-authors in the paper, “Influences of Printing Pattern on Mechanical Performance of Three-Dimensional-Printed Fiber-Reinforced Concrete.”
The filaments that Tran is using are as thin as human hairs, and make up two percent of the concrete. As the printer prints, these delicate fibers are stretched out in the direction the printer is moving. X-ray tomography has revealed the fibers stay oriented in different directions for different layers after the concrete hardens.
The result is a bioinspired concrete that’s 1.5 times stronger than a standard mix. But it’s not just superior in terms of brute strength. It also breaks better. When conventional concrete cracks, the fissures spread out in a plane, allowing them to extend deep into a structure.
“The fracture surface of bio-inspired concrete is twisted in a different direction,” said Tran. “It doesn’t go straight from top to bottom. Because a crack has to travel a longer path to complete the failure, more energy is needed to break bioinspired concrete.”
More for You: Diligence is Required When on the Hunt for Good AM Solutions
The results show promise for building components or infrastructure. But more work still must be done before it is put to use. The bioinspired concrete is fairly weak when still wet, so its use in structures is limited for now. Curved dome-like structures are similarly susceptible to gravity.
Rebar, of course, is used to strengthen concrete components and structures, but its use with this concrete still must be investigated. For the construction field, there are still limited studies investigating the changes of different internal architectures of cement-based materials on mechanical behavior, the authors noted.
Tran is thinking big, and looking to the heavens. He hopes his work will help change construction on this planet, but off the planet as well. “If you’re printing on the Moon or Mars, it needs to be fully autonomous,” he said.
Michael Abrams is a technology writer based in Westfield, N.J.
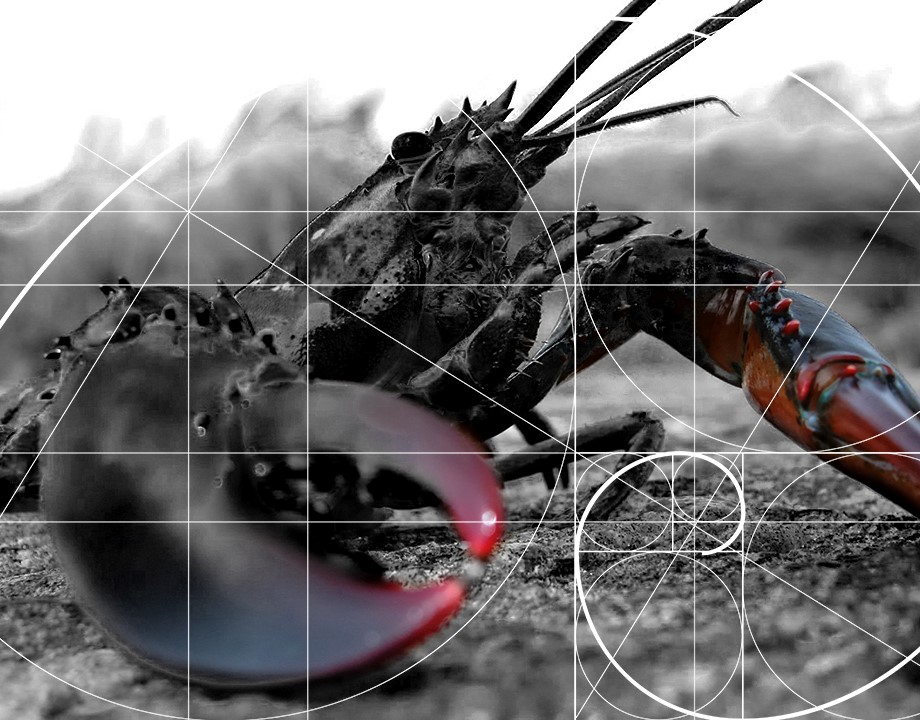
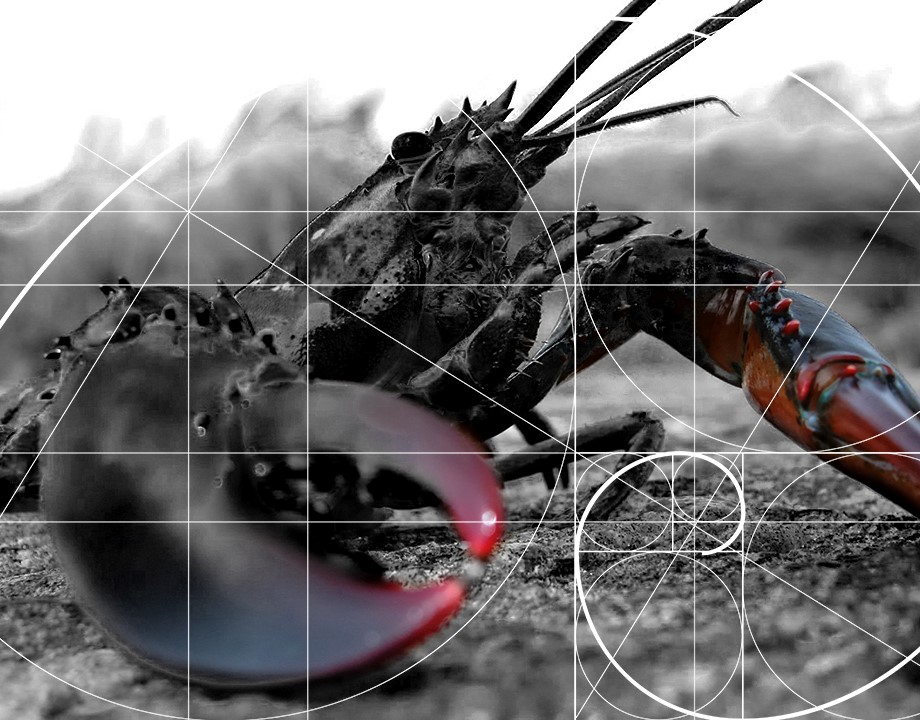