6 Insurances for Safe Hydraulic Hose Assemblies
6 Insurances for Safe Hydraulic Hose Assemblies
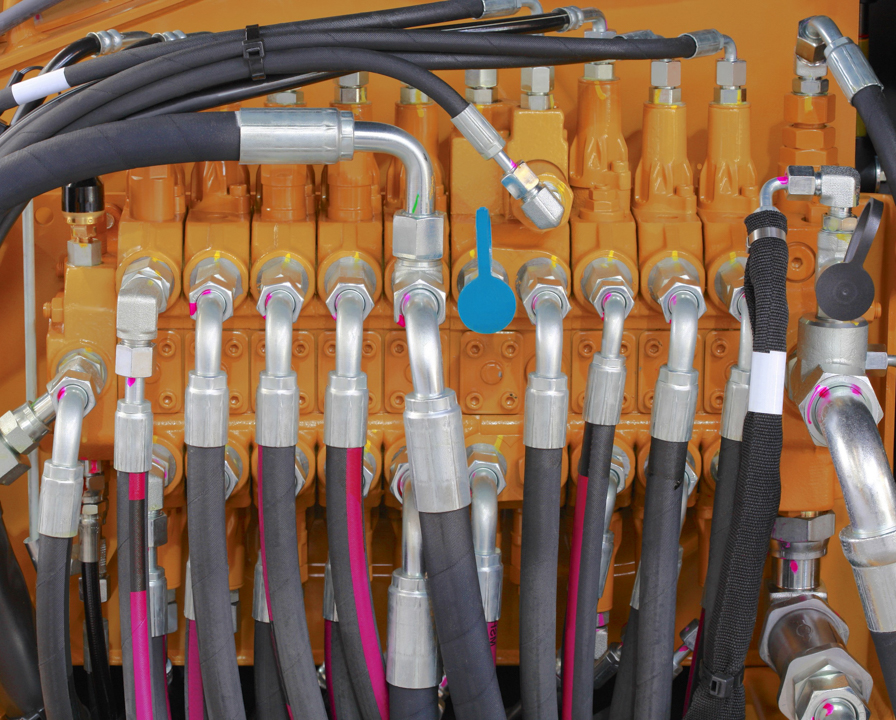
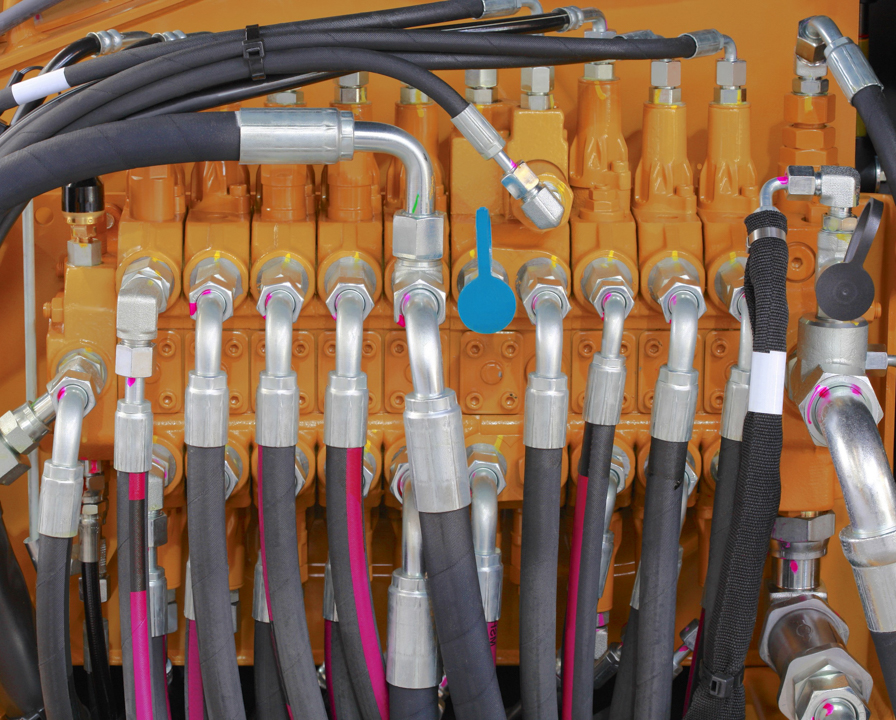
Great care goes into ensuring that electrical power stays inside electric cables. Likewise, great care should be taken to ensure that hydraulic fluid stays inside hoses.
When an engineer tries to search for information on “hydraulic hose installation,” they will find thousands of different sources and guides. Most sources outline best practices for safety and reliability. For example, hoses should be installed with enough slack to allow for expansion and contraction from pressure cycles. They should never be bent tighter than their minimum bend radius, and routing should prevent machine motion from causing twisting.
However, many applications require additional safety measures beyond these basics to prevent catastrophic failures that can harm equipment and people. A load unexpectedly dropping could sever a hose or cause it to separate from its end fitting. The result could be a serious accident causing severe damage to property and personnel. Even less catastrophic failures, such as a pinhole leak in a hose, can seriously injure people, or worse.
Although steel tubing is generally preferred for hydraulic lines, hoses are specified when fluid lines must be flexible to accommodate machine motion. Hose assemblies are also used when circuit lines must snake their way around and between obstacles within a machine. The complex bends and labor-intensive routing required in these instances can be impractical for steel tubing.
Fortunately, many solutions are available to help prevent these types of failures. Of course, they are not intended as a cure-all for any hose malfunction. Instead, each is designed to reduce or prevent the consequences of specific failures.
Because hoses are widely used where motion occurs, they can repeatedly rub against machine surfaces and other hoses. This is especially true in automated machines, where cyclical motion can cause premature wear from the hose continually rubbing against a potentially abrasive surface. And the presence of dirt, sand, or other contaminants only makes the problem worse. Most hydraulic hose manufacturers offer products with cover materials offering higher wear resistance than their standard products. But even this may not be enough in extreme cases.
1) Wear sleeves
For these more demanding applications, hose wear sleeves can provide additional protection. These sleeves fit over a hose — or several hoses — to act as a barrier between the hose cover and the machine surface. This type of sleeve not only prevents the hose from rubbing directly against an adjacent surface but also keeps several hoses bundled together and shields them from UV rays from sunlight, which could otherwise degrade compounds in the hose cover.
Listen to Our Podcast: The Unknown Strengths of Fluid Power
2) Spiral wraps
A similar type of hose protection is a spiral wrap. The wrap is made of a thermoplastic that has been pre-stressed to act as a spring to wrap around hoses easily. They provide less environmental protection that sleeves, wraps used primarily to keep several hoses bundled together. They are also quick and easy to install on existing equipment. Unless sleeves have a hook-and-loop or fastener along their length, they must be installed from the free end of the hose.
3) Heatshield sleeves
Even though best practices avoid installing hydraulic lines near a source of heat, sometimes, it cannot be avoided. Sometimes locating a hydraulic hose near a hot exhaust manifold may be the most practical route. For cases like these, a heat-resistant sleeve can be installed around the hose to shield it from the heat source. Of course, other safety measures should be explored for extreme cases like this, such as using a fire-resistant hydraulic fluid.
4) Safety sleeves
ISO 3457 and EN474-1 require that hydraulic hoses located within 1.0 meter of an operator and containing fluid at a pressure exceeding 5MPa (50 bar) or having a temperature exceeding 50°C, must be guarded. Safety sleeves are designed to contain pinhole leaks and bursts at high pressure to protect operators and other people within 1 meter of the hose. The sleeve also provides a channel to drain accumulated fluid from the sleeve. The feature not only prevents the sleeve itself from bursting but also provides a visual indication that the hose has been compromised.
You May Also Like This: Fluid Engineers Know How to Have Fun
5) Hose Restraints
Although accidents can occur in any application, some can be anticipated. For example, a log-harvesting machine could have a hydraulic hose pulled from its end fitting if a falling tree limb or other heavy object struck a hose. Depending on the circumstances, the free end of the hose could flail around wildly, spraying hot hydraulic fluid everywhere in the area. To prevent this from occurring, a restraint can be installed on a critical hose to restrict movement if it gets ripped loose. The restraint consists of a high-strength cable securely attached to the hose end and a stationary section of the machine.
6) Velocity Fuse
But the restraint alone may not keep fluid from flowing freely from the hose end. Some restraints may automatically shut off flow once the hose pulls loose. But if the hose itself is severed, the restraint will not terminate flow. For these cases, a velocity fuse can be specified to block flow if it detects a sudden flow surge. These devices are available with a variety of options, such as self-resetting capability, time delay, and for limiting volume or pressure.
Recommended for You: New Standard Simplifies Nonmetallic Pressure Piping Projects
Even though many of these solutions can prevent accidents from occurring, comprehensive training in machine operation and maintenance is still essential. This is especially true with hydraulic equipment because high pressure can still exist in-circuit lines even long after a machine has been shut down. Fluid trapped in a circuit can also allow a load to suddenly and unexpectedly drop if a valve or fitting is loosened by someone with inadequate knowledge of the system or proper safety practices for the machine.
Alan Hitchcox is an editor and technical writer based in suburban Dallas, Texas.
However, many applications require additional safety measures beyond these basics to prevent catastrophic failures that can harm equipment and people. A load unexpectedly dropping could sever a hose or cause it to separate from its end fitting. The result could be a serious accident causing severe damage to property and personnel. Even less catastrophic failures, such as a pinhole leak in a hose, can seriously injure people, or worse.
Although steel tubing is generally preferred for hydraulic lines, hoses are specified when fluid lines must be flexible to accommodate machine motion. Hose assemblies are also used when circuit lines must snake their way around and between obstacles within a machine. The complex bends and labor-intensive routing required in these instances can be impractical for steel tubing.
Fortunately, many solutions are available to help prevent these types of failures. Of course, they are not intended as a cure-all for any hose malfunction. Instead, each is designed to reduce or prevent the consequences of specific failures.
Building Safety into Hose Assemblies
Because hoses are widely used where motion occurs, they can repeatedly rub against machine surfaces and other hoses. This is especially true in automated machines, where cyclical motion can cause premature wear from the hose continually rubbing against a potentially abrasive surface. And the presence of dirt, sand, or other contaminants only makes the problem worse. Most hydraulic hose manufacturers offer products with cover materials offering higher wear resistance than their standard products. But even this may not be enough in extreme cases.
1) Wear sleeves
For these more demanding applications, hose wear sleeves can provide additional protection. These sleeves fit over a hose — or several hoses — to act as a barrier between the hose cover and the machine surface. This type of sleeve not only prevents the hose from rubbing directly against an adjacent surface but also keeps several hoses bundled together and shields them from UV rays from sunlight, which could otherwise degrade compounds in the hose cover.
Listen to Our Podcast: The Unknown Strengths of Fluid Power
2) Spiral wraps
A similar type of hose protection is a spiral wrap. The wrap is made of a thermoplastic that has been pre-stressed to act as a spring to wrap around hoses easily. They provide less environmental protection that sleeves, wraps used primarily to keep several hoses bundled together. They are also quick and easy to install on existing equipment. Unless sleeves have a hook-and-loop or fastener along their length, they must be installed from the free end of the hose.
3) Heatshield sleeves
Even though best practices avoid installing hydraulic lines near a source of heat, sometimes, it cannot be avoided. Sometimes locating a hydraulic hose near a hot exhaust manifold may be the most practical route. For cases like these, a heat-resistant sleeve can be installed around the hose to shield it from the heat source. Of course, other safety measures should be explored for extreme cases like this, such as using a fire-resistant hydraulic fluid.
4) Safety sleeves
ISO 3457 and EN474-1 require that hydraulic hoses located within 1.0 meter of an operator and containing fluid at a pressure exceeding 5MPa (50 bar) or having a temperature exceeding 50°C, must be guarded. Safety sleeves are designed to contain pinhole leaks and bursts at high pressure to protect operators and other people within 1 meter of the hose. The sleeve also provides a channel to drain accumulated fluid from the sleeve. The feature not only prevents the sleeve itself from bursting but also provides a visual indication that the hose has been compromised.
You May Also Like This: Fluid Engineers Know How to Have Fun
5) Hose Restraints
Although accidents can occur in any application, some can be anticipated. For example, a log-harvesting machine could have a hydraulic hose pulled from its end fitting if a falling tree limb or other heavy object struck a hose. Depending on the circumstances, the free end of the hose could flail around wildly, spraying hot hydraulic fluid everywhere in the area. To prevent this from occurring, a restraint can be installed on a critical hose to restrict movement if it gets ripped loose. The restraint consists of a high-strength cable securely attached to the hose end and a stationary section of the machine.
6) Velocity Fuse
But the restraint alone may not keep fluid from flowing freely from the hose end. Some restraints may automatically shut off flow once the hose pulls loose. But if the hose itself is severed, the restraint will not terminate flow. For these cases, a velocity fuse can be specified to block flow if it detects a sudden flow surge. These devices are available with a variety of options, such as self-resetting capability, time delay, and for limiting volume or pressure.
Recommended for You: New Standard Simplifies Nonmetallic Pressure Piping Projects
Safety Training is Essential
Even though many of these solutions can prevent accidents from occurring, comprehensive training in machine operation and maintenance is still essential. This is especially true with hydraulic equipment because high pressure can still exist in-circuit lines even long after a machine has been shut down. Fluid trapped in a circuit can also allow a load to suddenly and unexpectedly drop if a valve or fitting is loosened by someone with inadequate knowledge of the system or proper safety practices for the machine.
Alan Hitchcox is an editor and technical writer based in suburban Dallas, Texas.
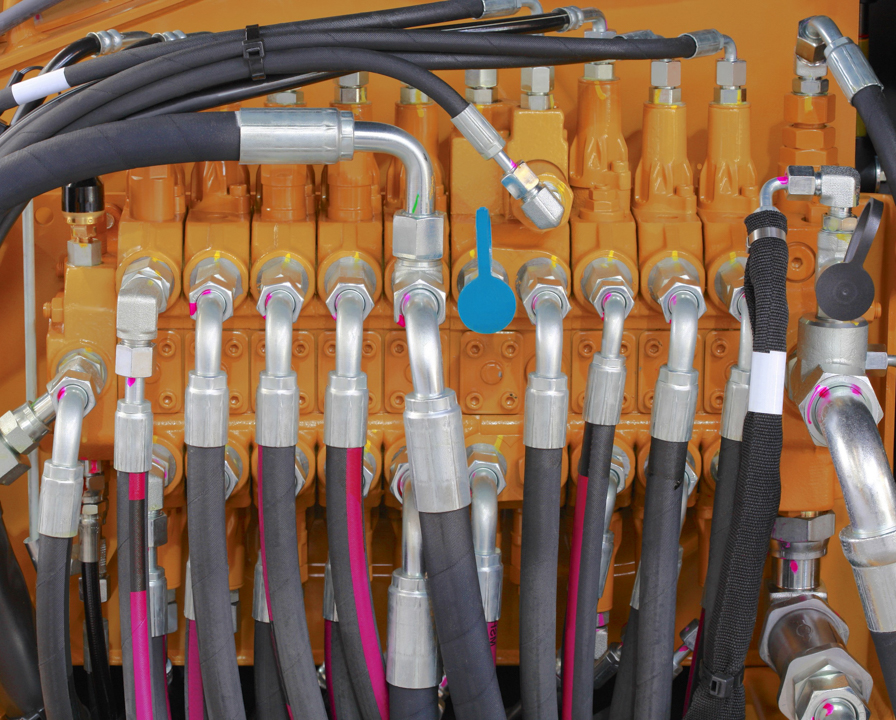
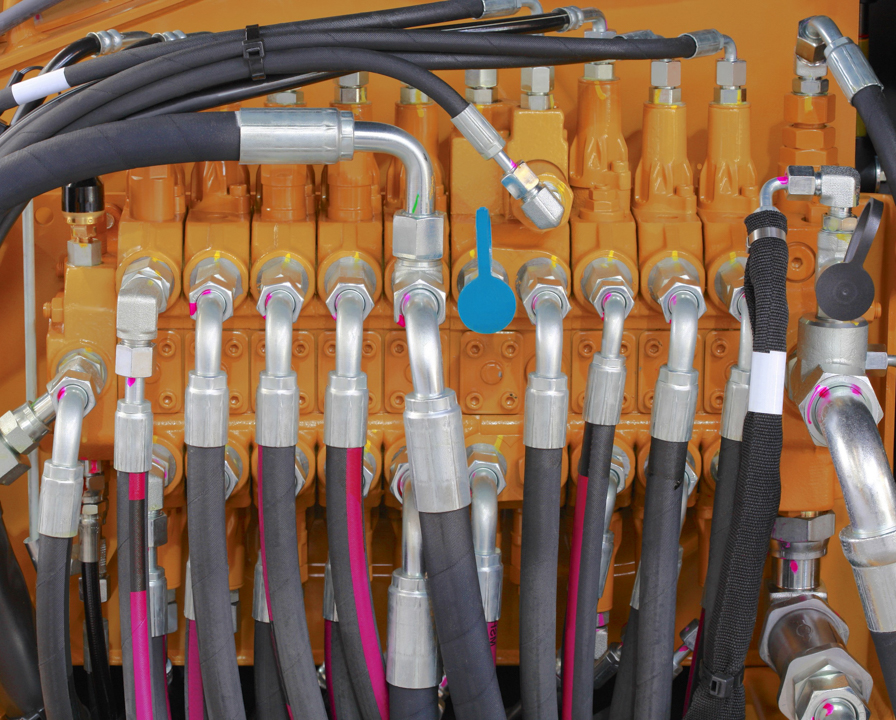