3D Printing at the Nanoscale
3D Printing at the Nanoscale
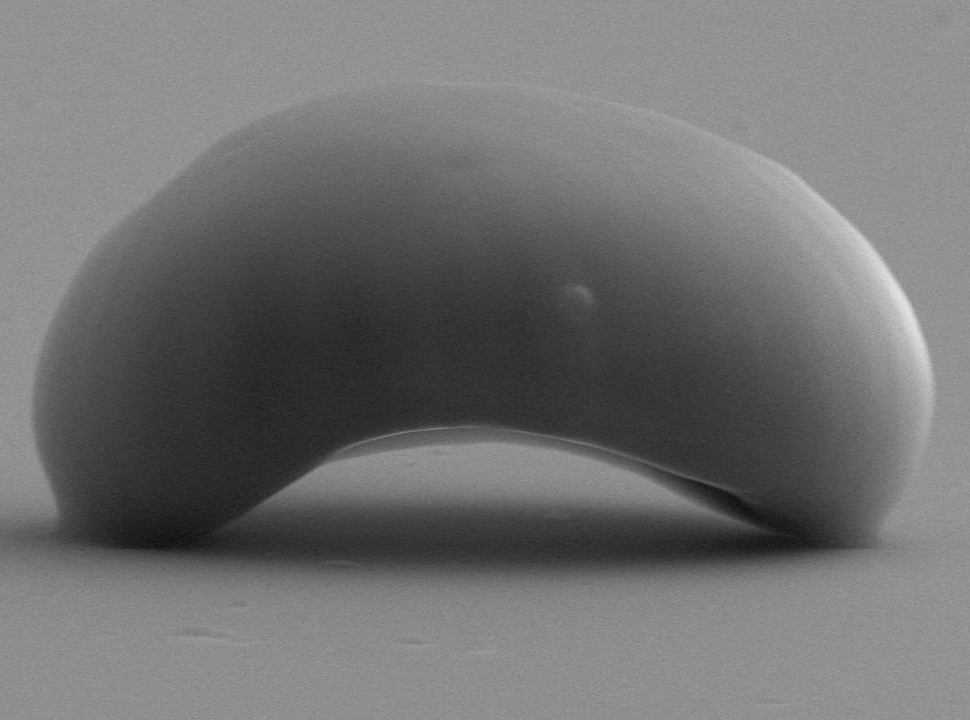
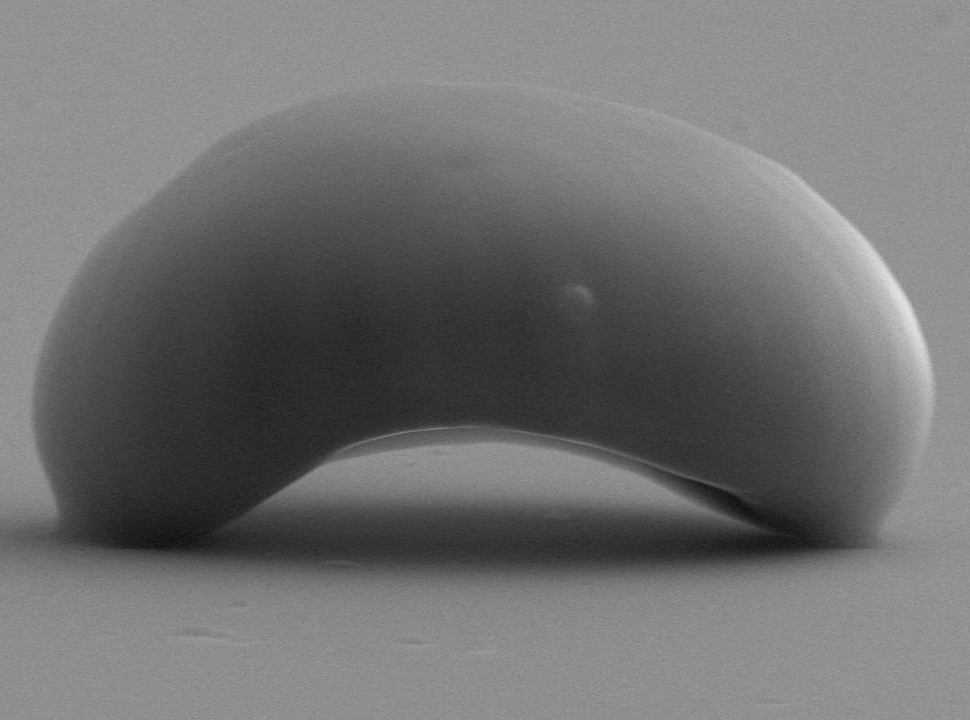
Nanomanufacturing technologies are creating complex, high-resolution nanostructures as thin as a human hair, with the goal of speeding and scaling the process for manufacturing industries.
Additive manufacturing (3D printing) continues to advance at a rapid pace—not just new types of technology and equipment that create highly complex products, but also much smaller ones.
For example, Xianfan Xu, a mechanical engineering professor at Purdue University, has created a 3D-printing system that can make complex objects that are less than the thickness of a human hair.
Xu’s system combines multi-photon lithography with spatiotemporal focusing of femtosecond laser pulses to generate rapid, continuous printing of complex 3D nanostructures. A volume of resin is exposed to a series of precisely focused femtosecond laser pulses, which causes the resin at the focal point to solidify almost instantly.
Continue Your Read: 3D Printing Overcoming Biocompatibility Challenge
By always moving the laser and/or the resin, 3D shapes can quickly be built at the nanoscale in a single continuous movement. Because these objects are smooth when finished, there is no need for secondary finishing operations, which add time and cost to more traditional 3D printing technologies.
How It Works
Laser-based manufacturing is an interdisciplinary area, involving optics, materials, control, and thermal engineering. “Mechanical engineers can find their skills useful in many of these areas,” said Xu. “It is necessary for the researchers involved in this work to apply not only the knowledge in their trained disciplines, but also incorporate many aspects in other disciplines to advance the technology.”Although multi-photon lithography has been known more than 20 years, its biggest drawback is that it is too slow for high-volume manufacturing. Xu’s goal is to speed up the process and its scalability, so that it can manufacture structures and objects with high precision and speed. This can be achieved by using temporal focusing, which separates the component wavelengths of a femtosecond laser pulse and then recombines them at a single plane.
Related Content: 8 Ways 3D Printing is Helping to Fight Coronavirus
The laser pulse becomes stretched in time when the component wavelengths are separated, reducing the pulse intensity,” he said. “As the pulse approaches the pattern plane, the pulse becomes shorter until it reaches the focus, where all the component wavelengths recombine to form the shortest, highest-intensity pulse.”
A digital micro-mirror device (an array of tiny mirrors controlled by a computer) separates the laser into multiple wavelengths of light then recombines them to focus on the area of the resin to be solidified. An entire 2D layer can be printed instantly while physically moving the platform up and printing another horizontal layer.
This is a huge advantage over typical 3D printers, where the object is printed layer by layer, often leaving irregular or jagged edges that then must be removed or smoothed through secondary processes. Xu’s system doesn’t start and stop. Instead, it moves continuously, creating one smooth shape all the way up. This results in faster printing of complex shapes and geometries, with no attendant layering artifacts.
“The system is fast,” said Xu. “Complex nanoscale 3D geometries, including smooth, curved surfaces were fabricated in a continuous fashion on the millisecond timescale.”
Keep Reading: Metal 3D Printing for Orthopedics
Future Possibilities
“To make nanomanufacturing practical, we have to optimize time and scale,” said Xu. “Creating a single nanostructure in a lab, over several days, just doesn’t scale. With this technique, we can make nanoscale 3D printing practical for biomedicine, micro-robotics, optics, consumer products, and more.”The biggest surprise for Xu was how far his team could push high-resolution 3D printing to achieve such small and detailed features. “We are continuing to improve and refine our technology,” he added. “One of our goals in the next few years is to further improve the printing speed and expand the use of the technology to manufacturing in industry.”
Mark Crawford is an independent writer.
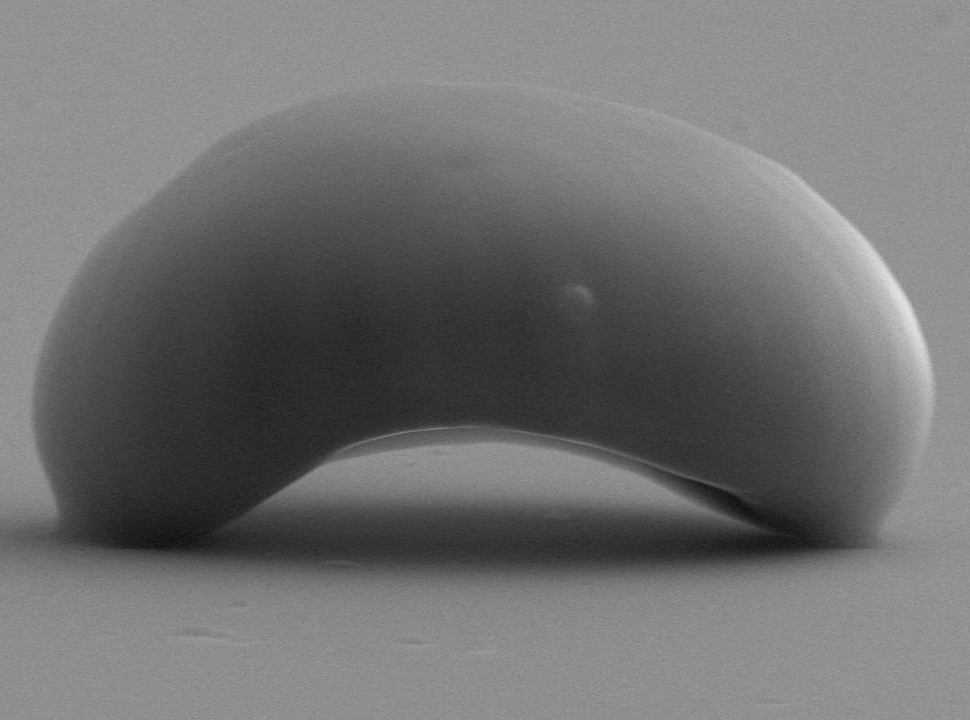
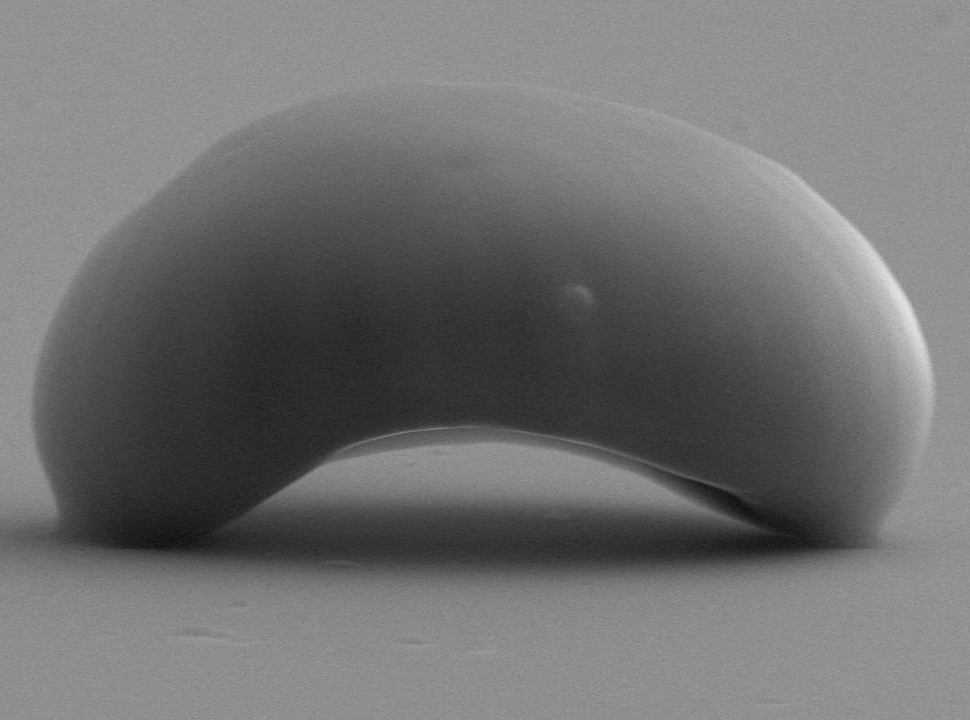